Sound privacy and noise level are among the qualities occupants are least satisfied with in existing buildings. More shocking than this is the relative lack of research into aural comfort compared to related topics like visual and thermal comfort. With this in mind, we decided to use our existing FabLAB space with its very noisy CNC Router as a testing ground to develop tools and strategies applicable to the larger practice of architecture for addressing aural comfort.
These physical studies expand on past CNC tests and digital simulations. The new geometries push the limits of our fabrication capabilities and test out some novel machining approaches. We set specific goals and restrictions on the project to ensure our results would be relevant and applicable to the architectural typologies on which our firm focuses – i.e. Science and Healthcare. We set criteria that our solution be build-able and made from durable and cleanable materials. We also took this as an opportunity to develop digital tools to assist in the design and assessment of our studies resulting in grasshopper logics, fabrication techniques and verification algorithm being developed.
Over the past few months, we’ve been developing a new iteration of acoustical mock-ups, building on our previous physical studies and digital simulations. In the video above, we’re flip-milling (cutting both sides of the material) 6″ thick high-density foam. After cutting the back-side, this timelapse shows us milling the front, with custom surfacing toolpaths in evidence. Careful planning and alignments were needed to achieve the slit apertures that you see here.
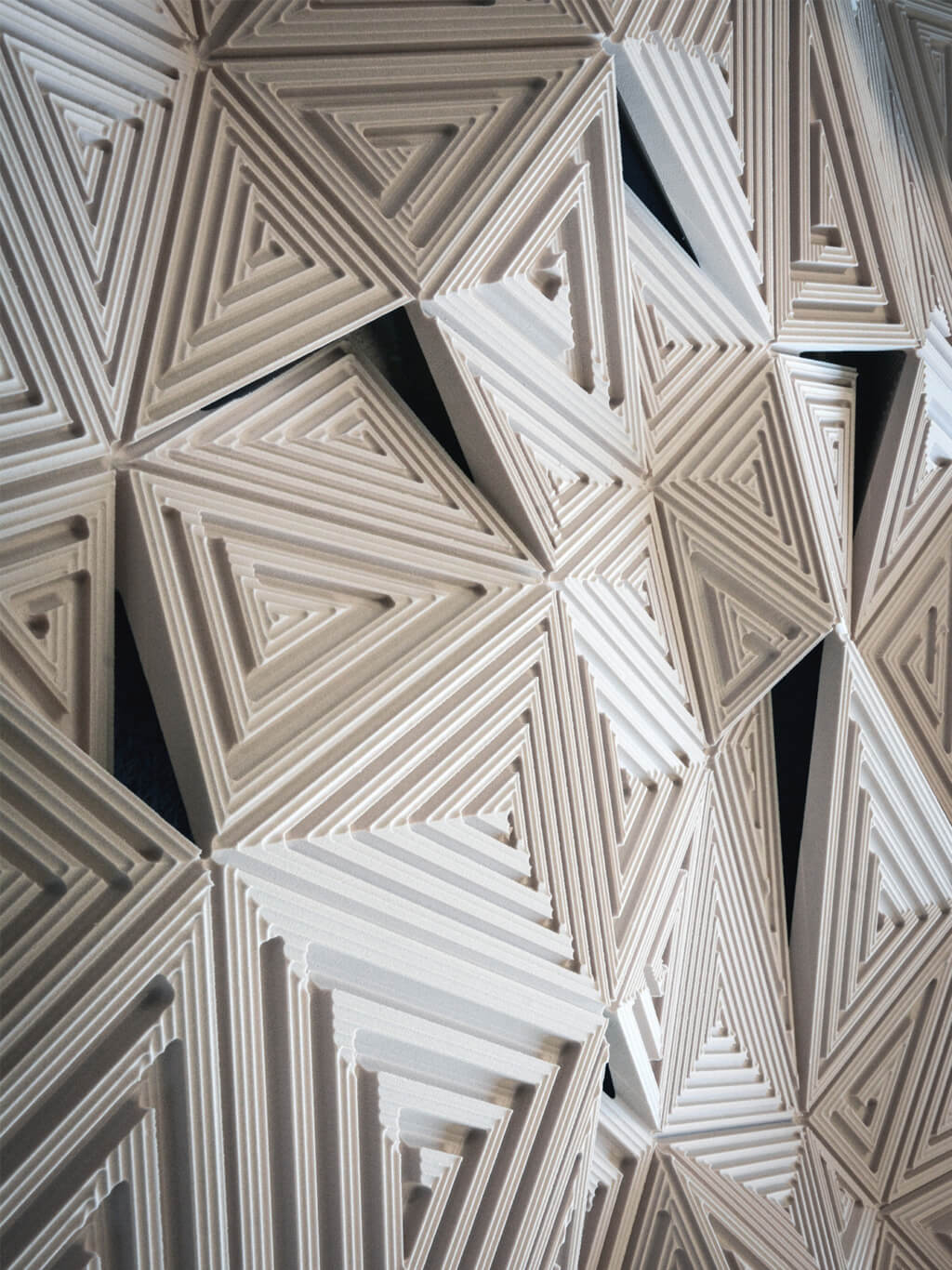
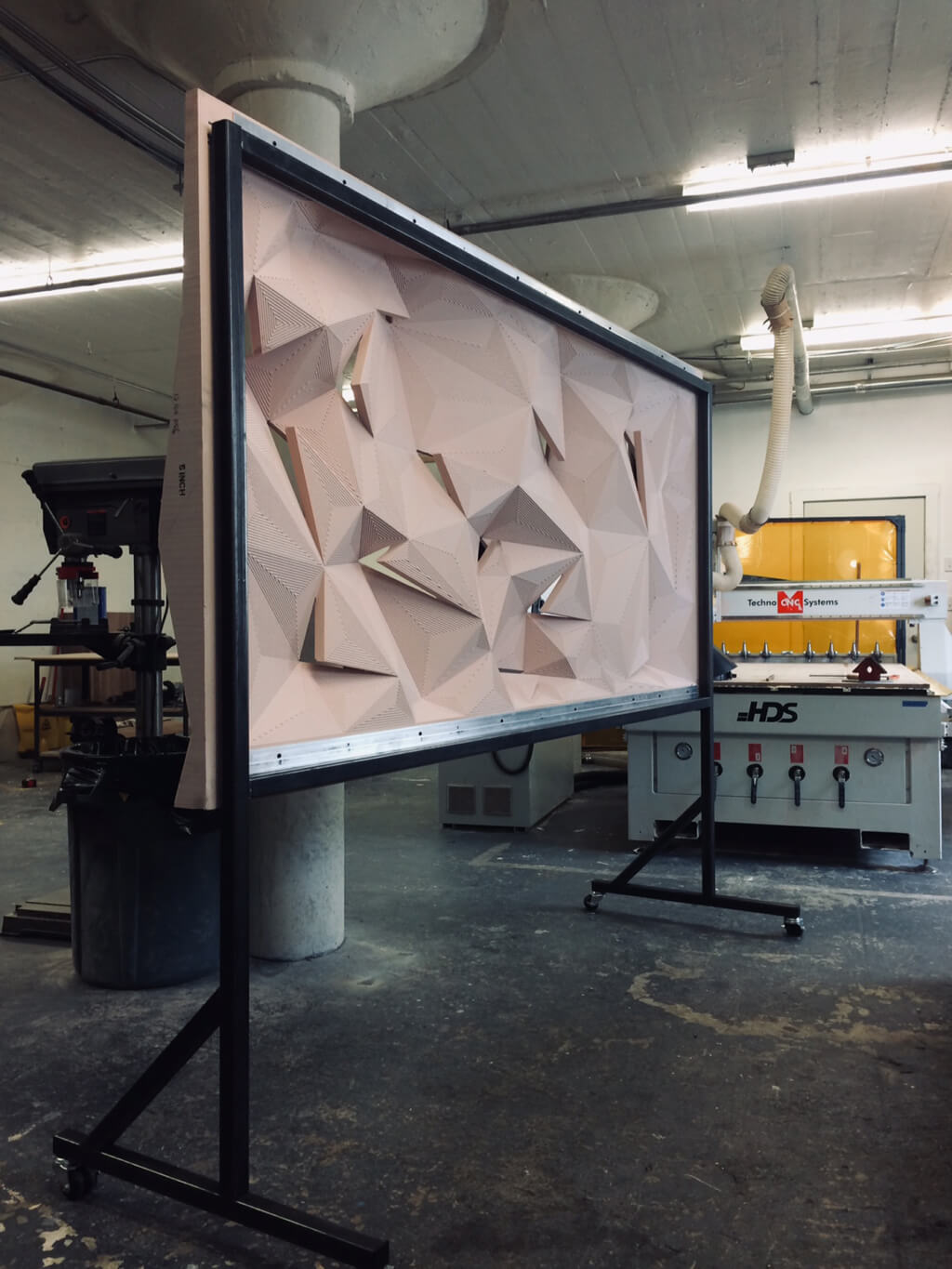
This mockup was featured as part of the Exhibit Hall at ABX 2018 earlier this fall.
PAYETTE team: Dane Clark, Luke Gehron, Garrett House, Parke MacDowell, Tanguy Marquis, Eric Rigo
Related Links:
The Geometry of Sound Diffusion
The Materiality of Sound Absorption
Optimizing the Location of Absorptive Geometries for Aural Comfort