In August, five designers from PAYETTE traveled to Buffalo, NY to attend the fourth annual Architectural Ceramics Assemblies Workshop (ACAW) hosted by Boston Valley Terracotta and the University at Buffalo School of Architecture.
The mission of the workshop is to foster open-ended exploration of the use of glazed terracotta in high-performance facade design. Representatives from the industry and academia came from around the world to gather for the weeklong event, with teams constructing a mock up from their prototypes, and presenting their studies to peers in the industry.
Using the full palette of technical capabilities available at BVTC, UBSAP and SMART, participants were given the opportunity to collaborate in the co-creation of ideas and tactics aimed at achieving a deeper understanding of terracotta and developing a vocabulary for working with the material. We participated in this event to increase our knowledge of terracotta as a material, and the various fabrication techniques and glazing processes involved in its production, while engaging with designers from other well-known architecture practices. This year, ACAW hosted nine firms from around the country including SHoP, KierranTimberlake, SOM, KPF, HKS/Line and Pelli Clark Pelli, as well as two academic teams.
ACAW has established itself as one of the most unique workshops internationally. This is evident in part by the requirement that teams begin preparation for the event up to six months prior to attending. The prep work is intended to provide a dialogue with the fabricators to assist the design teams to solidify their concepts, receive feedback related to the production process and to fine-tune a prototype that will be fabricated in advance of the event. This allows the workshop itself to be focused more on exploring new practices and researching and designing ways to facilitate communication between industry, practice and academia.

The PAYETTE team this year included Luke Gehron, Parke MacDowell, Craig Mutter, Sarah Solomon and Jensen Ying. Using the geometric exercise from our ongoing acoustic research as a jumping-off point, we developed a prototype for a wall panel, and used the preparation phase to modify and optimize the panel’s shape through an iterative design process and correspondence with BVTC for the terracotta manufacturing process and glazing techniques. By the time the workshop started, the panels had been fabricated and glazed and were ready for us to assemble and make any final changes to the pieces.
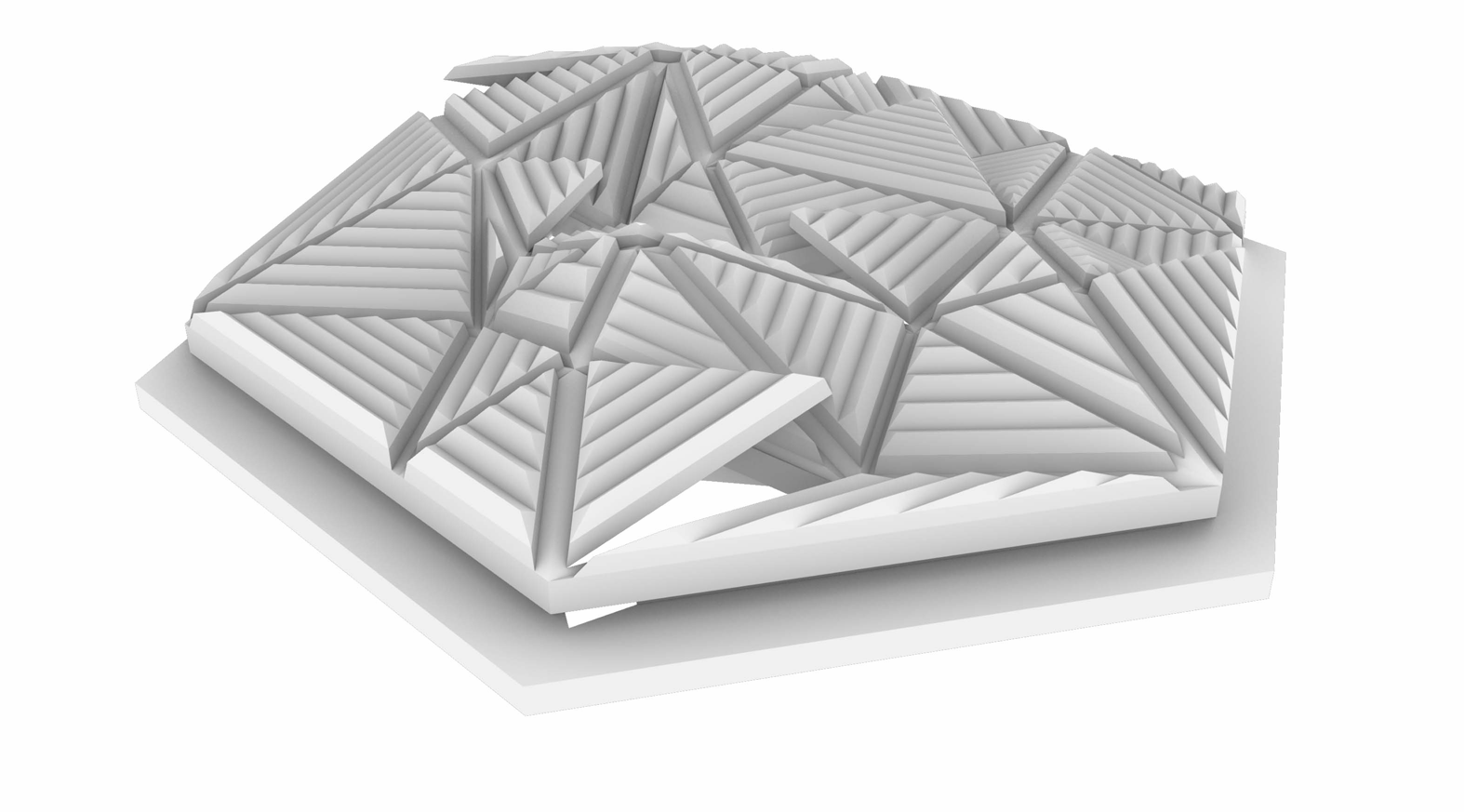
The four-day workshop was comprised of a full day tour, two days of intense production and a final day of presentations and a reception. The tour offered an extensive exploration of the Boston Valley Terracotta facility, where all phases of terracotta manufacturing processes were presented, and the tour ended with an in-depth look at the glazing techniques. The facility revealed the level of craft and manual intervention some of the pieces of terracotta required for particular projects, where craftsmen and ceramists could be seen on the shop floor meticulously detailing and post-processing the terracotta. The possibilities of designing terracotta pieces and glazing were far more extensive than we had previously imagined. The experience was made us think about how we could work with the material in the future.
Upon seeing our terracotta panels in the workshop on the second day, we decided to add backlighting. We focused our work with this goal in mind. The team split up to take on several tasks: constructing and painting the frame, cutting the edges of our terracotta pieces to appropriate lengths, making a supply run to Home Depot and assembling the presentation for the final day. We also hosted a mini-workshop to show our two grad student assistants from the University at Buffalo the techniques used to generate the panel form in Rhino/Grasshopper. Once everything had been prepared, the last step was to add the lights and mount the panels on the frame.

On the last day, we put the final touches on our presentation and set up our display booth where we featured our final board, an iPad with image slide of the build process, a spare panel showing the underside of the structure and some off-cuts which allowed us to discuss the glazing techniques of pooling, pin-holing and breaking. Each team was then given ten minutes to present their process and findings to the larger community of architects and academics.

Overall the workshop was a uniquely collaborative opportunity that synthesizes the skills of manufacturers, fabricators, designers and engineers for a common purpose. We worked with many talented and knowledgeable people, and witnessed the workflows of other great architectural firms trying novel assembly and manufacturing techniques with terracotta. As it was our first year at the workshop, we played to our strengths and created a piece we were very proud of. Next time, we hope to experiment more. Our efforts culminated in an impressive and a successful piece; we were highly praised by the organizers for our novel use of mold release and glazing.
Next year, we hope to find a group of talented individuals to follow-up and create another great project. The organizers and presenters were very passionate about exploring the possibilities of the material, and this energy resonated throughout the entire workshop. Their expert knowledge about a material with such an unpredictable nature was astounding, and they encouraged the participants of the workshop to continue to explore and push the boundaries of what the material is capable of producing.