Design for Deconstruction (DfD) is an architectural design approach that aims to economically recover resources and maximize the reuse and recycling of materials at the end of a building’s lifecycle. Unlike the linear model of extraction, production, use and disposal at landfills, DfD envisions a circular loop of use and reuse. DfD considers the entire lifecycle of a building and its materials early in the design phase, focusing on easy disassembly, material separation and recovery of valuable resources. Some of the principles and strategies for Designing for Deconstruction are summarized in the image below.
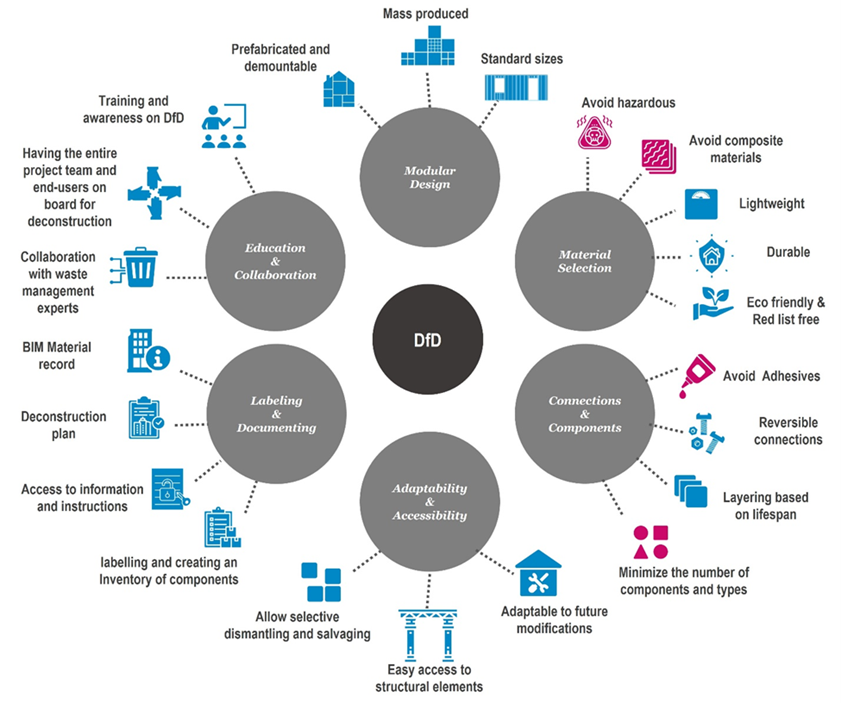
At PAYETTE, we design buildings to last for future generations. Yet each building has its life span, ranging from 50-100 years or even more. As buildings reach their end of life, the question of “what do we do with the building materials” becomes urgent. As part of our research effort on material reuse and circular construction, we want to highlight how the Sustainable Engineering Labs project at UMass Amherst applies Design for Deconstruction principles to ensure long-term flexibility and promote material circularity. Successful implementation of DfD strategies involves the designer, contractor and owner.
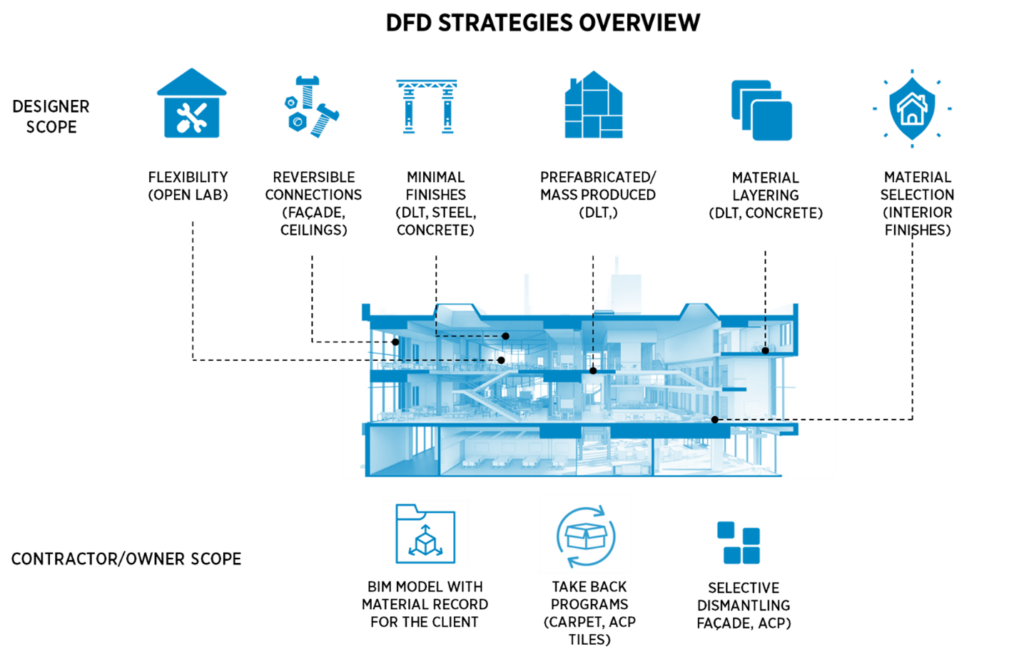
The project team consciously eliminated the use of any extraneous materials or assemblies throughout the project which not only reduces costs and carbon emissions but also eases future deconstruction and maximizes material recovery. By Designing for Deconstruction, end-of-life emissions of project materials are avoided whenmaterials are recovered and salvaged. Let’s dive into different elements of this project to learn where and how the DfD strategies have been implemented in the design documents.
Flexible Open Workshop
The flexible open workshop space with suspended raceways hanging from the ceiling makes it easier to move all the casework and reconfigure the space easily for any future expansions with minimal demolition. The MEP design of the lab space also includes extra capacity for any future renovations or a new program.
The exposed ceiling with bolted structural connections makes it easier to disassemble and reclaim the steel structure for reuse after deconstruction compared to welded connections. Reusing steel instead of recycling can save up to 70% of primary energy and avoid up to 80% of carbon emissions (Broniewicz, E. and Dec, K., 2022).
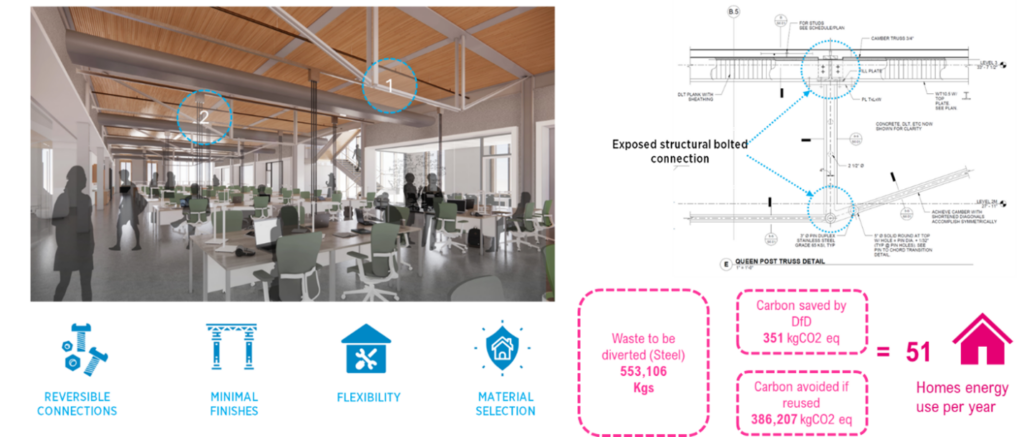
Acoustic Dowel Laminated Timber Floor System
The dowel laminated timber (DLT) panels are prefabricated modules connected with dowels instead of adhesives or fasteners. The exposed panels with minimal finishes layered on top of the acoustic mat and plywood sheathing minimize potential damage during deconstruction and enable efficient material recovery. Even though the concrete topping slab can only be recovered for recycling, the material layering helps with maximizing the reuse of the DLT. The incorporation of acoustic insulation in the DLT itself avoids the need for acoustic ceilings in most of the labs, commons and offices spaces, fully eliminating the cost and future waste of finish ceiling assemblies.
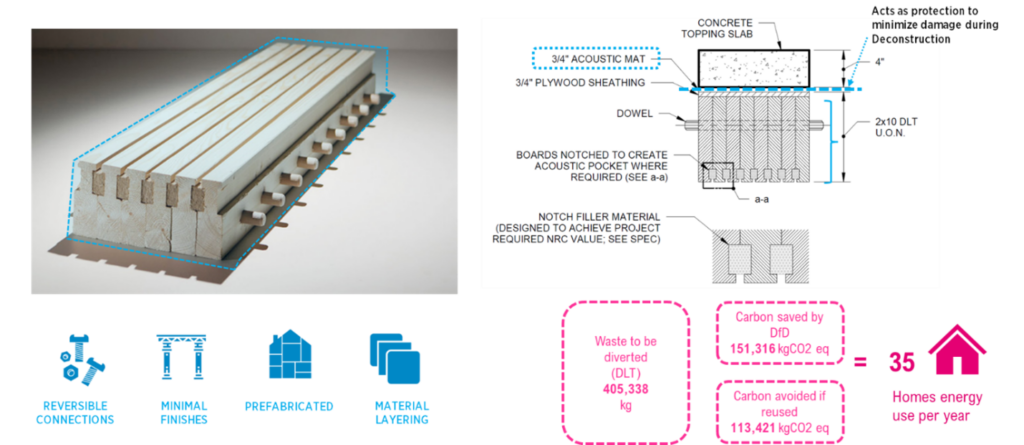
Interior Finishes
Minimal finishes (e.g., exposed concrete floors and interior walls) wherever possible reduce the number of components to be deconstructed and eventually reduce the time and costs typically associated with disassembly. The team selected red list-free and eco-friendly materials to ensure the materials could be reused. Acoustic ceiling tiles, aluminum panes ceilings, markerboards and loose-laid carpets come in standard sizes and use reversible connections that can be easily disassembled and reused in other projects. Other ceiling options including mineral wool, Gypsum, fiberglass boards and fixed carpets can be recycled through manufacturer take-back programs. Gypsum board partitions are designed to have minimal finishes, this minimizing contamination and maximizing recovery for recycling. Total waste diverted, including reuse and recycling, is – 719,251.64 kg, and carbon saved by reusing the ceiling tiles = 13,754 kg co2 eq.
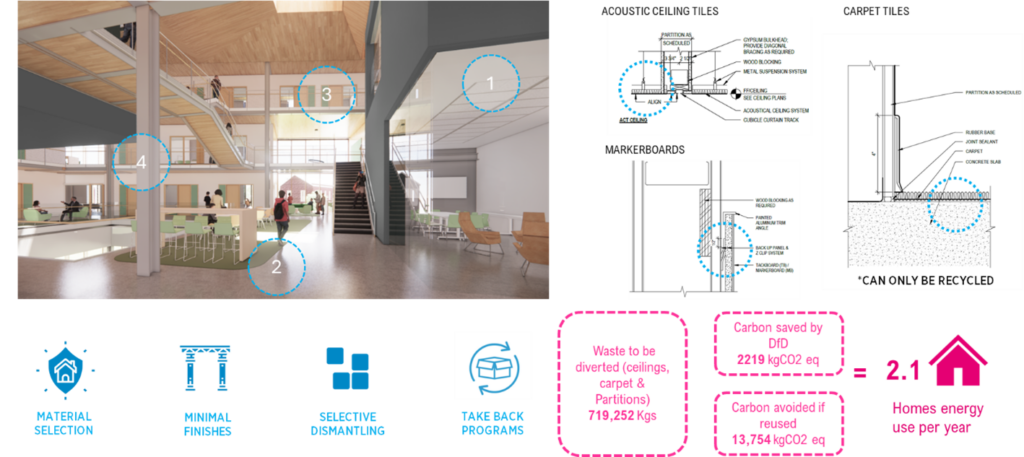
Exterior Fins
The exterior metal fins are mounted to the façade using reversible connections, which enables selective dismantling for easy repairs and replacement in the future. Only the damaged or required assemblies would be removed instead of replacing the entire façade. The fins are made of durable materials, mass-produced and prefabricated, to ensure the quality and quantity requirements for future reuse.
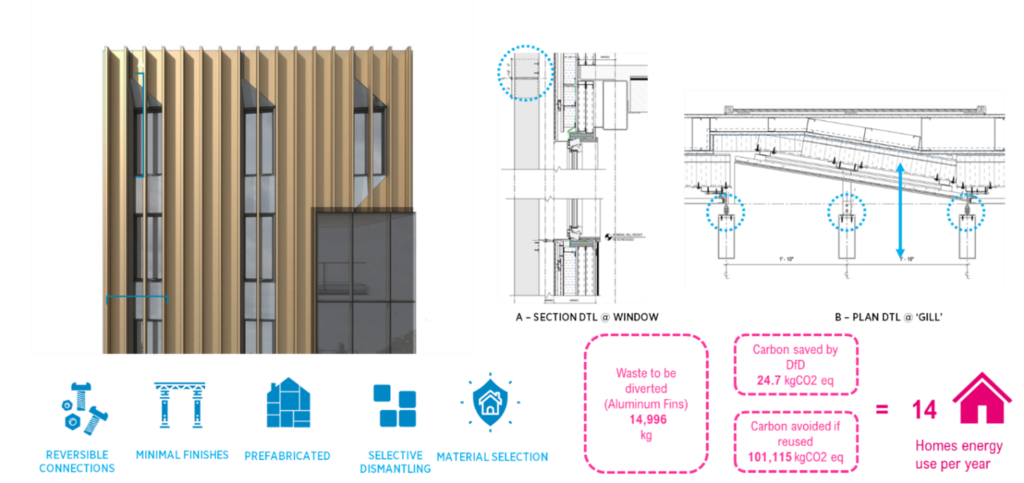
Future opportunities
Looking back, the project successfully integrates sustainable strategies with quality design within a compressed schedule and tight budget. We are eager to test out even more strategies and have identified several Design for Deconstruction opportunities that could be further explored in the following section.
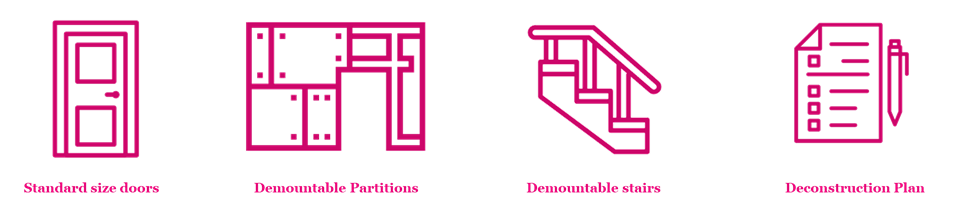
- Standard Size Doors – Due to this project’s skip-stop and floor height limitations, having standard size doors was not feasible. While the nonstandard doors in this project are still demountable, standard size doors tend to have higher demand for salvage, and we could design around the idea of uniformity and modularity in other projects where appropriate.
- Demountable Partitions – Although demountable partitions tend to cost more, they are a great alternative to conventional wood stud walls, allowing flexible space configuration and easy dismantling and reassembly. The open lab space in this project minimizes the need for partitions and therefore does not need demountable partitions but for future projects we could think about how to strategically use demountable partitions to maximize their value.
- Demountable stairs – Welded stairs have lower initial carbon than demountable stairs with reversible connections, but when reused, there are higher carbon savings for the demountable stairs. Reusing stair components, i.e., treads and guardrails, can be a future design idea to test out.
- Deconstruction Plan – Full deconstruction plan can be explored, including a range of action items such as clean-out and soft stripping and the more complex task of removing structural elements. Creating a deconstruction plan often requires slight additional cost and time but ensures a higher rate of material recovery at the end of life. (Hennepin County, 2024). It will be an interesting challenge to manage cost and time and introduce the benefits of deconstruction plan to our stakeholders.
Design for Deconstruction is still a relatively new concept in the construction world. With the UMass SEL project, we are excited to implement the DfD strategies and inspire peers in the design and construction industry to embrace Design for Deconstruction as an important sustainable, zero-waste strategy.
Reference
- Broniewicz, E. and Dec, K., 2022. Environmental impact of demolishing a steel structure design for disassembly. Energies, 15(19), p.7358.
- Hennepin County. (2024). Project Manager’s Guide to Material Reuse in Commercial Buildings. .
- Bertino, G.; Kisser, J.;Zeilinger, J.; Langergraber, G.; Fischer,T.; Österreicher, D. Fundamentals of Building Deconstruction as a Circular Economy Strategy for the Reuse of Construction Materials. Appl. Sci.2021, 11, 939. https://doi.org/10.3390/app11030939
- Kanters, J. (2018). Design for deconstruction in the design process: State of the art. Buildings, 8(11), 150
- Tzourmaklioutou, D. (2021). Designing for deconstruction-The related factors. J. Civ. Eng. Archit, 15, 459-468
- https://content.aia.org/sites/default/files/2020-03/ADR-Guide-final_0.pdf
- https://www.paperturn-view.com/?pid=MjY266316&v=2.2
- Icons – https://thenounproject.com/