Laevitas: an ephemeral glass skin
In crisp contrast to the built-up masonry façade, the highly-transparent, minimally-detailed ‘double-skin’ façade announces ‘Science on Display’ from the northwest campus approach. This broad face also fronts the renewed Wesleyan Place – a landscape courtyard centered between New Science and the renovated Shanklin Hall (McKimm Mead and White, 1928). While inviting observers into the building, this façade also pushes the interior atrium space that binds the three research clusters outward into the public outdoor realm. This west-facing glass volume engages in a direct relationship across the exterior space from to Hall, whose image will be clearly reflected in daytime conditions.
Beyond transparency, the double-skin façade plays an important climatic role – a thermal blanket in cold weather, providing a cooling stack effect in warm weather – while balancing natural lighting and glare control.
Wesleyan University is in Middletown, Connecticut roughly one-hundred miles northeast of New York City. Located in Climate Zone 5A, the site has warm summers with very few extremely hot days, dry with cold winters with prolonged periods of snow cover, and relatively mild spring and fall with warm days and cool evenings.

The 185,000 GSF New Science Building replaces two of Wesleyan’s outdated facilities with a unified building that integrates life science programs under a single roof. The building aims to be an exemplar of sustainability and energy performance with an pEUI of 86 kbtu/sf/yr, 75% less than the AIA 2030 baseline building of this typology.
The west-facing orientation of the glass wall posed a challenge for the design team in achieving in the desired visual transparency and connection between the Commons and Wesleyan Place. Each afternoon throughout the year, the highly transparent façade would be subject to direct sunlight leading to glare and radiant discomfort for occupants as well as increased peak cooling loads during the summer months.
Additionally, the desire to reduce annual heating loads meant that any large, glazed façade had to perform substantially better thermally than a standard aluminum curtain wall system.

The initial solution to the challenge of glare and peak loads was a fixed external metal mesh which could diffuse the direct afternoon sunlight. Coupled with a high-performing triple-glazed curtain wall system, this approach addressed both peak load and annual heating challenges. However, the static nature of the mesh meant that transparency and visual connection between the Commons and landscape was severely compromised.
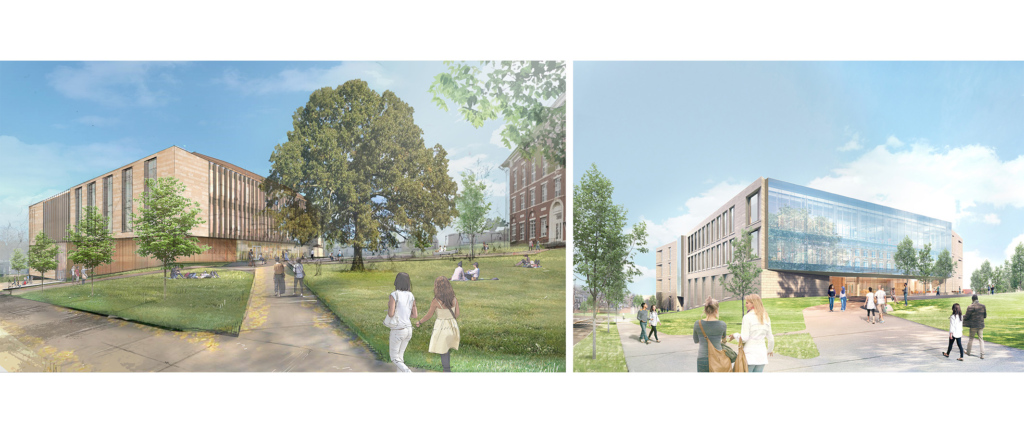
The desire for a dynamic shading system – one that responded to sun orientation and sky conditions – drove the team to start looking at double-skin façade systems. Exterior dynamic shading systems in New England are subject to snow and ice during the winter months, so locating the shading systems within a ventilated cavity affords protection from the elements in winter while still achieving the benefits of reduced solar heat gain in the summer. With the exterior blinds protected in a semi-conditioned cavity, the natural next step for the team was to leverage the airspace as a thermal buffer in winter and to extract heat away from the façade in summer. With buy-in from Wesleyan, the team moved ahead changing the design after the schematic design phase of the project.
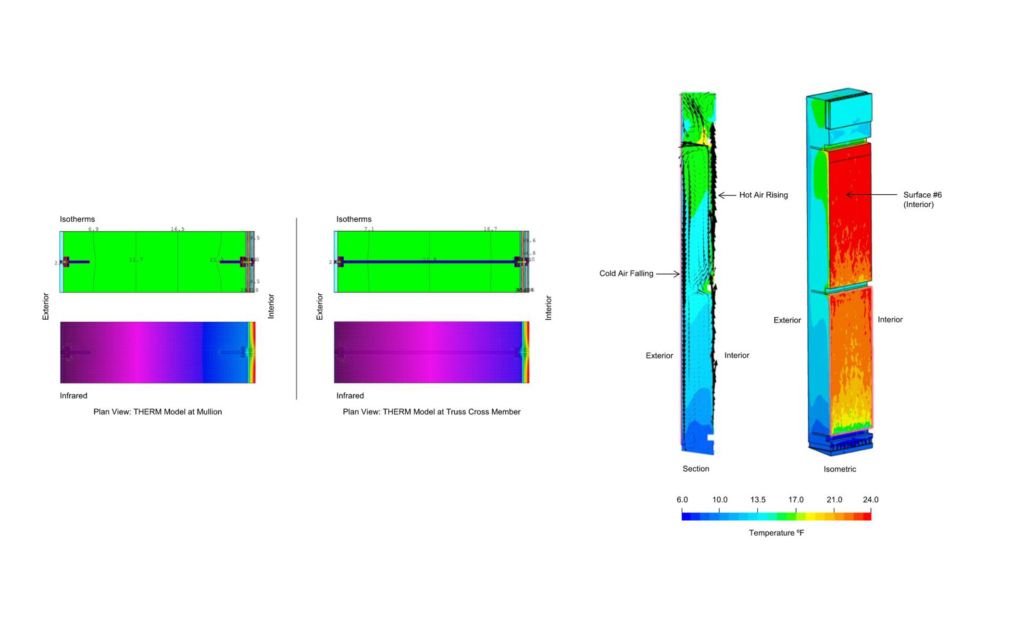
The resulting design of the Wesleyan double-skin façade is two stories tall by 140ft wide, comprised of an interior triple-insulated glazing unit, a 42-inch ventilated cavity with access catwalk, and a laminated glass exterior. The glass is retained to a precision-fabricated steel truss through toggles on the vertical mullions and structural silicone on the horizontals.
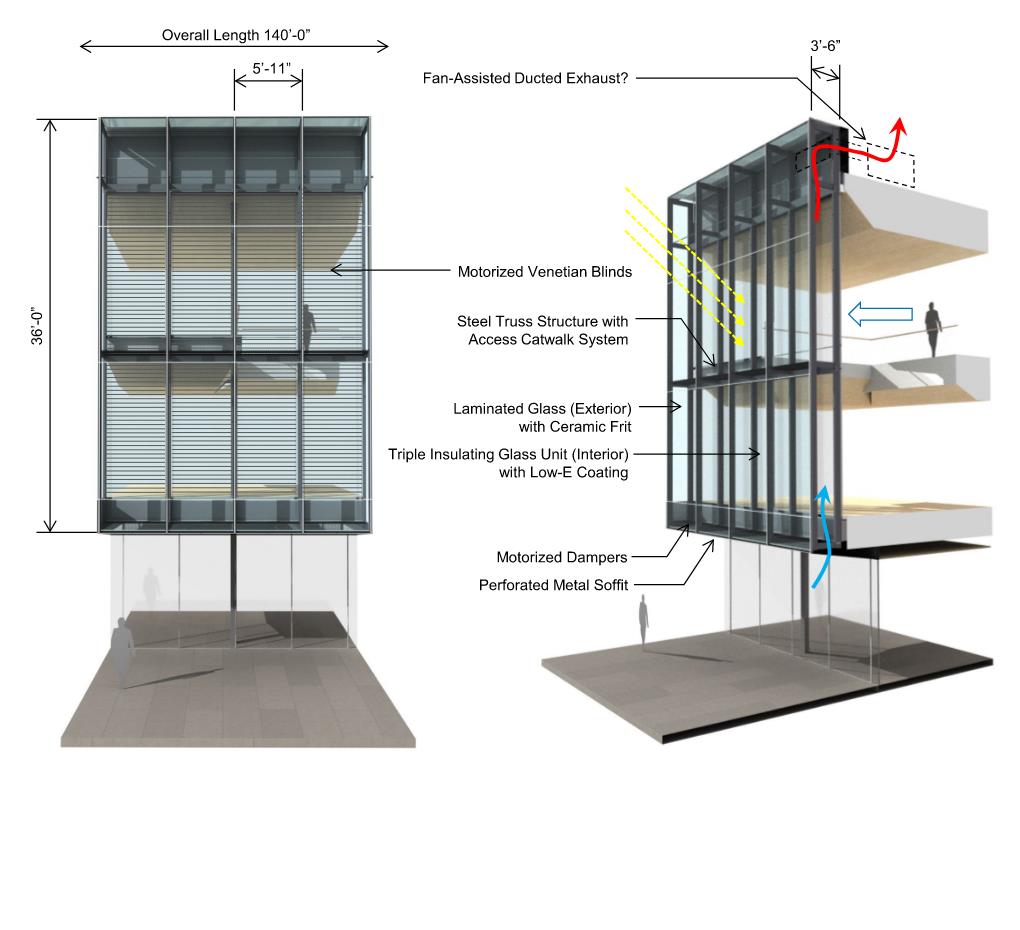
The bespoke steel and aluminum façade elements were pre-fabricated in Germany by Josef Gartner in Gundelfingen an der Donau (roughly 50 miles from where our Jura Limestone was quarried), assembled for fit, then disassembled and packed for shipment to the site. Preparing the attachment points at the west slab edge required weeks of fine calibration to reconcile the shop drawings with the allowable steel and concrete construction tolerances. But after this process, the actual installation of the metal components took only days – hoisting the double-height trusses to the outrigger attachment points and tying the system together with the smaller, mechanically fastened lateral components.
Once the internal skeleton of the assembly was in place, glazing began with the interior units (which serve as the primary perimeter thermal and moisture barrier) and then the bird-fritted laminated exterior units. At almost 18’ tall, these outer panels push the limits for what is commercially produceable – the system culminates in the minimal silicone joint that speaks to the exacting coordination and quality control process.
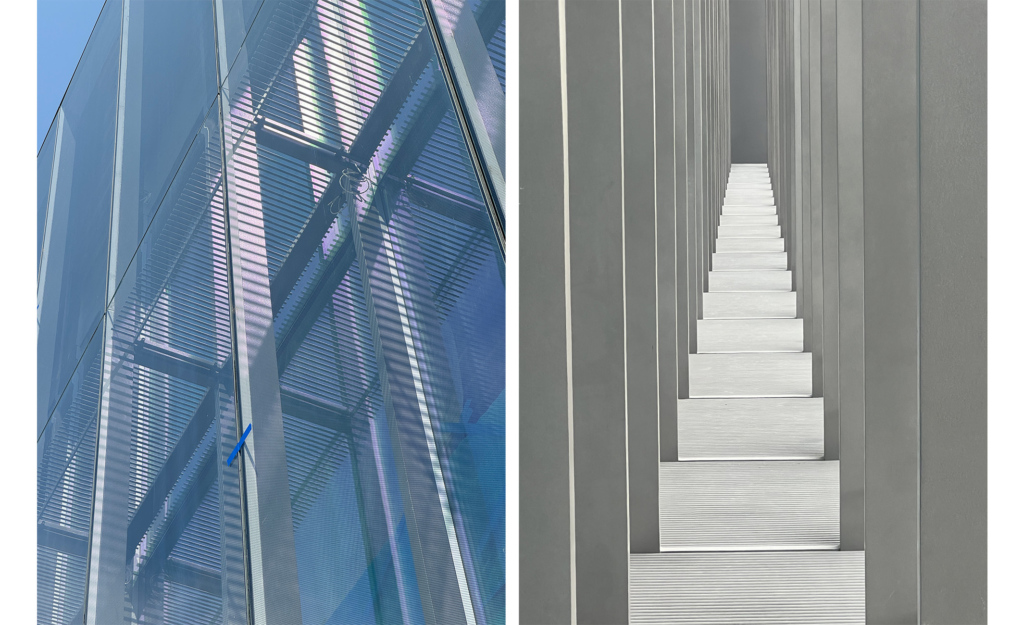
Last to be installed are the automated louver blinds, which will be tied into the building automation system and roof-mounted daylight sensors, to complete the west-facing assembly this Spring.
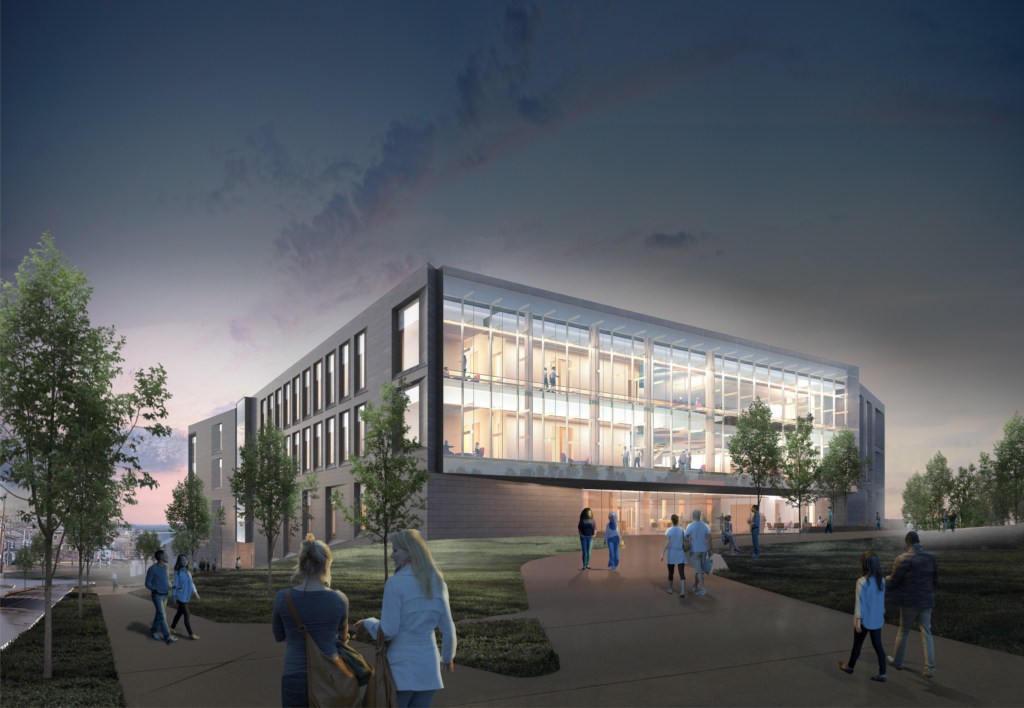