Recently, the BCH Needham team had the opportunity to travel to Arriscraft’s Georgia facility to assess the color and variation of the brick destined for the new Ambulatory Care Facility in Needham, Massachusetts. Read on to learn more about Arriscraft’s innovative approach to brick manufacturing as well as their QA/QC process specific to our project.
At the heart of Arriscraft’s business model is the precise mix of ingredients that compose their brick: 92% silica sand, 6% lime, and 2% oxide pigments. All Arriscraft stone and brick products follow this composition, ensuring consistency and quality. Silica sand, accounting for over 90% of the product mass, is locally sourced within a 20-mile radius, while lime is typically sourced from Alabama or West Virginia. This is what makes the plant’s location in Fort Valley, Georgia so ideal.
Before forming silica sand, lime, and oxide into bricks, these materials undergo several processes. The silica sand is carefully screened to remove any aggregate over 3/16”, ensuring uniformity in texture. Lime is then layered onto the sand before entering a large reactor bin where the lime hydrates and heats up. Oxide pigments, which determine a brick’s color, are then mixed thoroughly with the sand-lime blend before going into the press cycle.
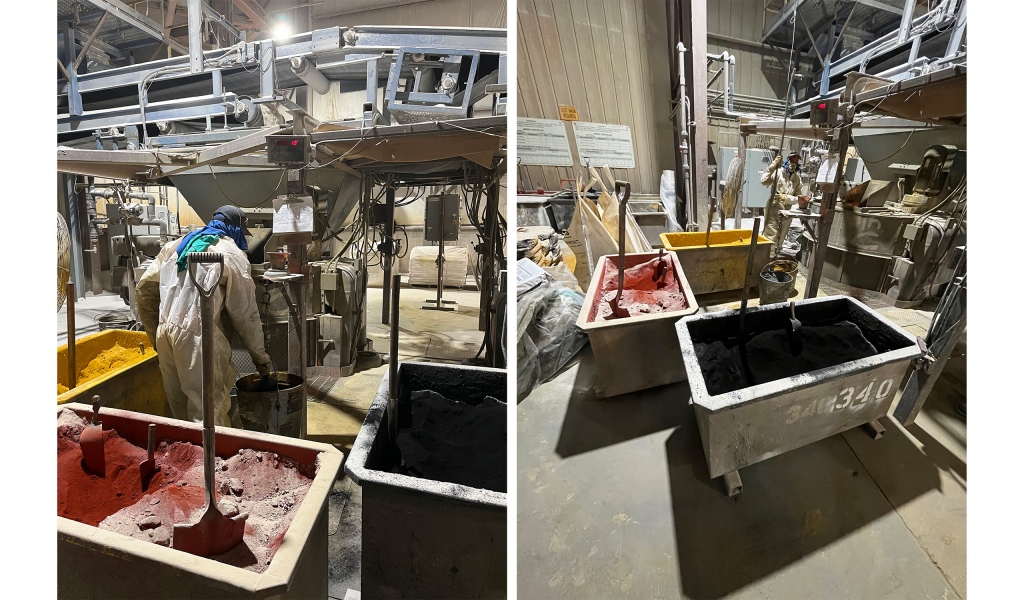
The press cycle shapes and presses the mix into brick units, after which these units are placed into autoclaves for 8-10 hours, where a chemical reaction occurs under high-pressure steam. This reaction, facilitated by the lime, fuses the sand particles together, creating what is known as a calcium silicate hydrate binder. This process mimics the natural geological processes that create limestone and sandstone over millions of years!
Once brick units have left the autoclave, they are further cleaned, finished and refined with water and cutting tools. In addition to sourcing local materials, Arriscraft also demonstrates their commitment to sustainability by recycling all water used on site. The water used in cutting stone and cooling down diamond blades on saws is recycled into settling ponds on-site. These ponds allow sediments to settle naturally, enabling the water to be reused multiple times. Additionally, steam is recycled from one autoclave to the next, reducing natural gas usage.
Furthermore, Arriscraft minimizes waste by repurposing discarded materials. Any waste from the manufacturing process is crushed into ¾” rock, bagged, and sold to the local landscaping industry. This recycled material is used as a gravel mowing strip around buildings and gardens, providing an eco-friendly alternative to traditional mulch.
After a thorough tour of Arriscraft’s facilities, the BCH Needham team was able to inspect specific bricks from our project’s production run. During design, our team opted for the Architectural Linear Series Brick in a Cedar Woods color: a cool, dark-gray brick with expressive texture and variation. Moreover, the linear and random pattern of the brick units will allow the finished project to give both a geological and timeless impression.
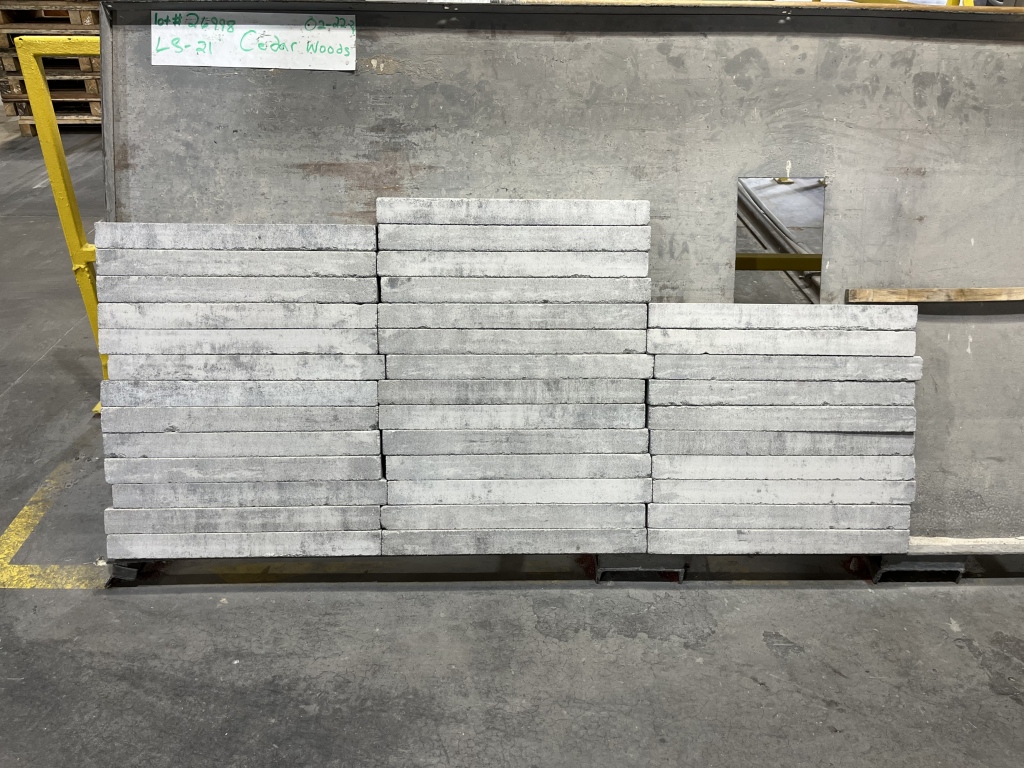
In the photo above, several brick units from multiple days are shown stacked together. This enabled us to confirm that consistent variations of lighter and darker bricks were being produced over the course of several days and weeks. It is also important to note that after erection, the brick will be washed with a calcium silicate cleaner (EaCo Chem Solution 4:1) that will draw out the natural texture of the brick, resulting in a higher contrast façade with an overall darker appearance. Separate from the stacked units, Arriscraft also allowed us to open and inspect pallets of brick ready for shipment. Among these bricks were custom-cut units to be featured at our project’s signature projected soffits.
Overall, the trip enabled our client to feel more comfortable about the color and quality of the brick soon to arrive at their site. Arriscraft has been diligently taking random color chip samples from each rail car and comparing the samples to previous runs for consistency, absorption and compressive strength. Lastly, they have even taken care to send periodic production photos to PAYETTE and the general contractor, Turner.
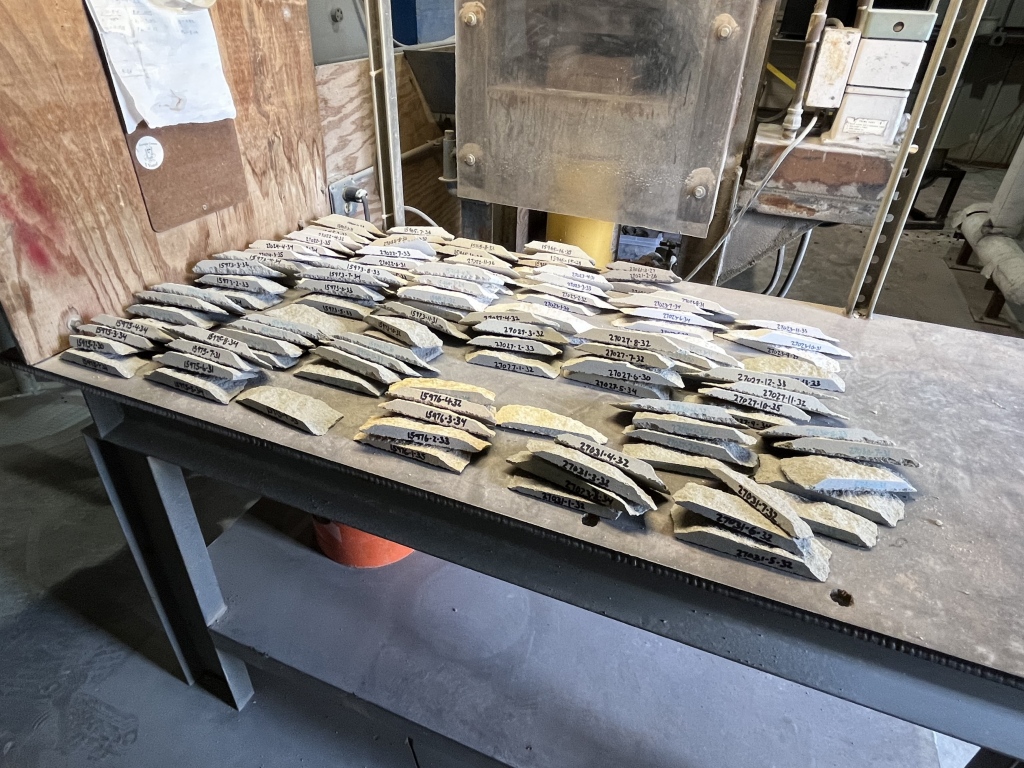
PAYETTE would like to extend our gratitude to Arriscraft as well as Consolidated Brick for organizing and hosting such an insightful trip!