Models are vectors that convey architecture to people, and each model PAYETTE’s fabrication team realizes is a project of its own. Whether the building is already built or still in the design stage, it must go through a new set of peculiar model construction phases to come to life. Once an appropriate scale is agreed upon, we determine which fabrication strategies to use, the detailing and assembly sequence of each component, evaluate our finish options and more. As any design process, we go back and forth between these steps and our craft evolves as we experiment and develop novel constructive techniques. Although each piece is made with a specific approach, the intent of model making is always to communicate and showcase the key elements of the project to an audience.
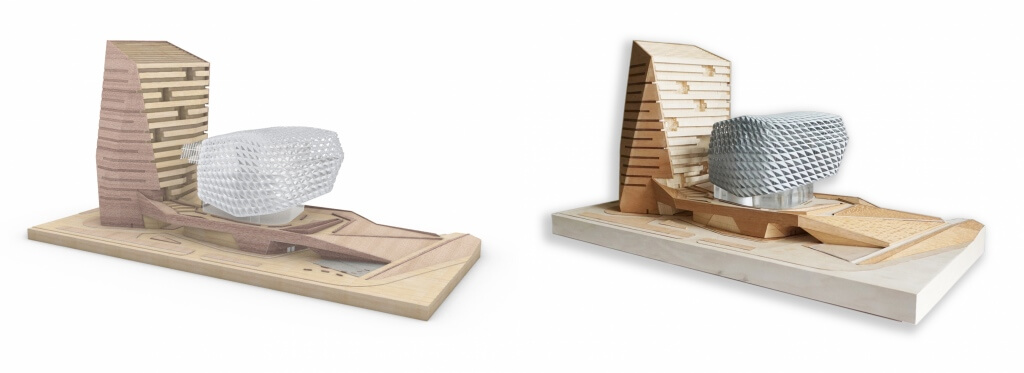
In the case of an exhibition model, where the resulting product is final and meant for a larger audience, every element is represented with the highest possible finish quality. PAYETTE’s latest model, depicting the Hengqin Innovation Center located in Zhuhai, China, is now ready to steal the spotlight at an exhibition. Two main features stand out in the composition of this project: the tower, a solid volume emerging from the plinth, connected to the surrounding landscape; and the jewel, a distinct, light and floating object. Expressing this concept was the starting point of the model. Once we had a starting point, the fabrication team began the process of creating the model, and documented tricks and the magic we went through to bring this beautiful project from the digital into the physical world.
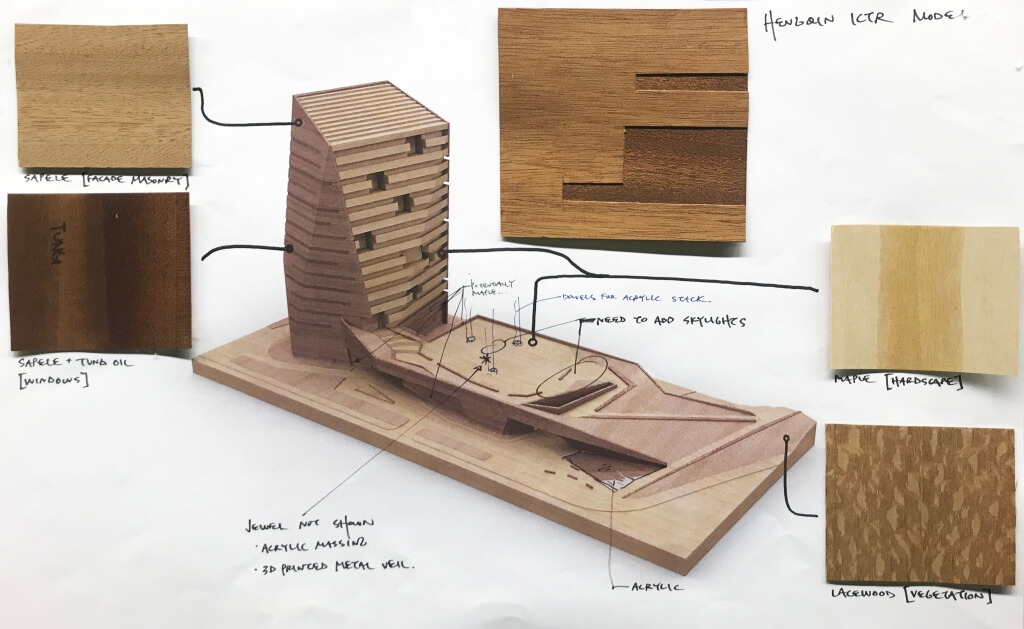
We began with cleaning the project file and translating it into simpler shapes, to get a better understanding of what needed to be made. When this was done, we discussed finish options and fabrication strategies that best suited this building with the project team. For this specific model, we rendered different iterations of the model using scans of actual veneer for texture mapping. These images helped us and the project team clarify our goals and vision for the overall look of the model.
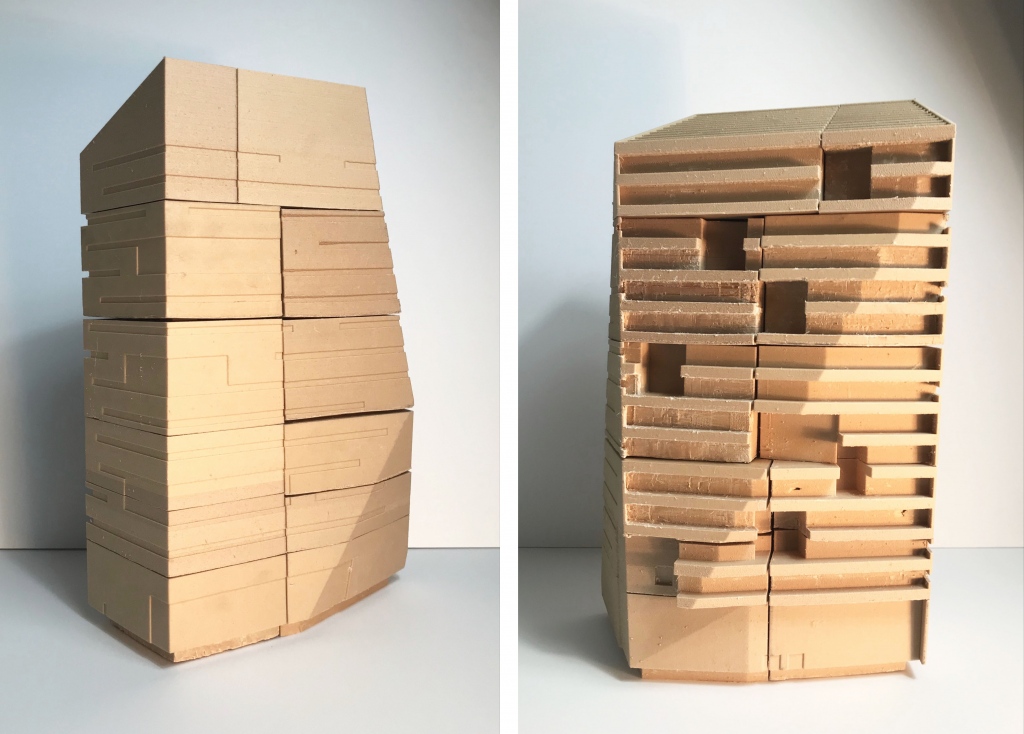
The virtual model was subsequently separated into multiple parts and adjusted accordingly with the machine used to fabricate it. Interlocking joints and other details were created to facilitate the upcoming assembly. Prototypes of sections and finishes tests were executed to validate each decision and constructive strategy. Throughout this process, constant coordination was essential between every person involved in the fabrication of this model to ensure an optimal fit and avoid any defects.

Although the purpose of this model was to evoke the idea of a single sculpted piece, its fabrication required different materials and the use of all the machines we have in house. The base was made from high density foam milled with the CNC, the tower and the plinth were 3D printed and assembled like construction blocks and the inside of the jewel was made of laser cut and milled acrylic layers. A 3D printed veil, outsourced because of its size and materiality, completed the components of the model. After the fabrication came post processing steps including filling gaps and sanding to remove any imperfections left by the digital tools used. A dry fit of all the elements ensured everything brought from the model to the physical world respects its original dimensions before proceeding further.
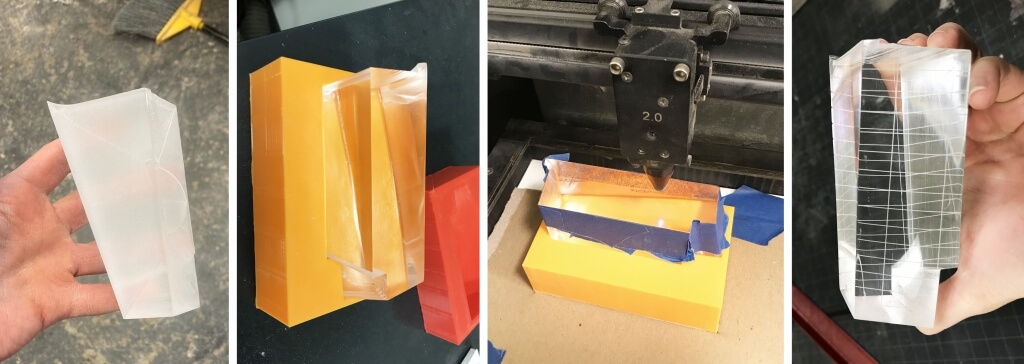
The bridge linking the tower to the jewel, needed its own share of attention. Several quick 3D printed plastic iterations were needed to create the correct geometry. When the exact fit was achieved, a more detailed version with clear resin was printed to include the mullions. Four bridges later, the production of the final piece was ready to commence. It was CNC carved from a flip-milled solid piece of acrylic, to obtain the same language as the inside of the jewel, hand polished and then laser engraved using a custom jig to lay it flat on the machine’s bed.
Then began the meticulous covering of the tower and the plinth with the right essence of laser cut veneer, with a special consideration for the direction of the wood grain. A consistent finish throughout the model was crucial to attain the illusion of a single piece. Every piece of veneer was then oiled for the finishing touch.
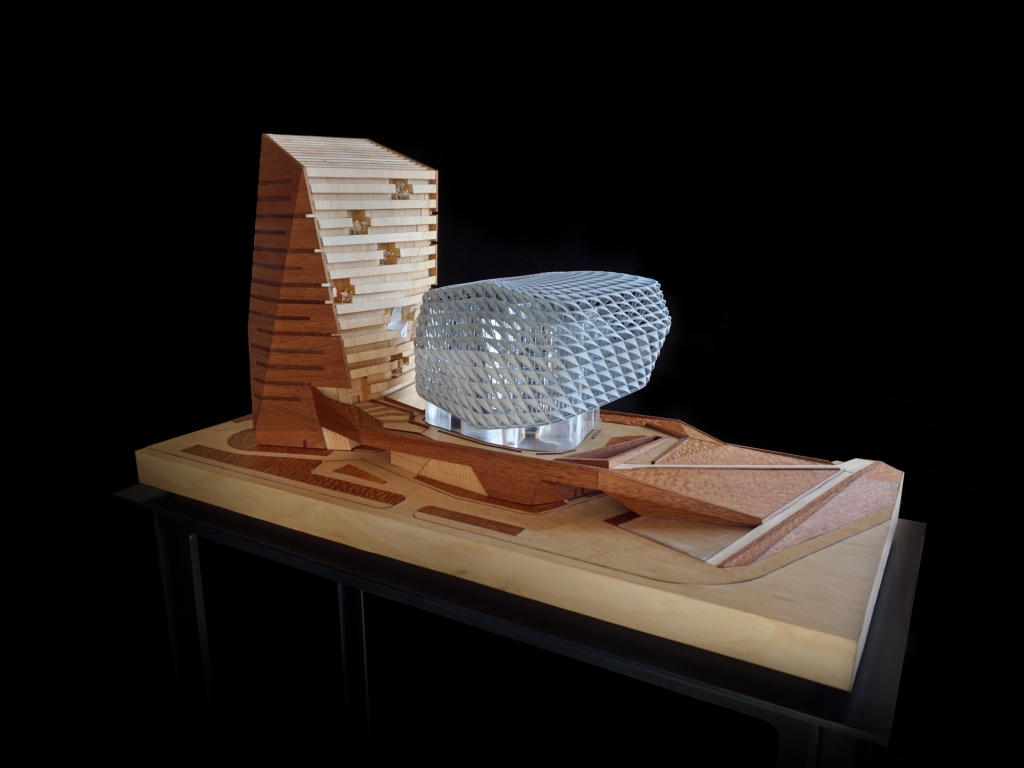
Once the plinth and tower were in place, the layers of acrylic composing inside of the jewel could be assembled. They were stacked up and held in place by translucent dowels, positioned where the vertical cores of the building are located. The 3D printed veil fully encapsulates the heart of the jewel and was compressed between the first layers of acrylic, whose shape acts as a receptacle. Once the bridge was in place and the top part of the veil attached to its other half, the assembly was complete. The Hengqin Innovation Center 1:200 model stands proudly on its custom made steel table and is ready to be the center of an upcoming exhibition!