Room mockups are an extremely beneficial tool when implemented early in the design process for healthcare projects because it allows staff, end users, project stake holders and designers to analyze a design and develop an optimal solution. By experiencing a space at full scale, the nuances of the design can be studied in more detail that otherwise may be missed or misunderstood through two-dimensional drawings. The targeted goals of building mockups include:
• Understand room size and maneuverability within the room
• Confirm room layout meets client and user needs
• Confirm appropriate equipment and furniture is provided and placed in desirable locations
• Confirm electrical outlets, switches, light fixtures and medical gas quantities and locations
• Ultimately save time, reduce risk and possible changes during construction
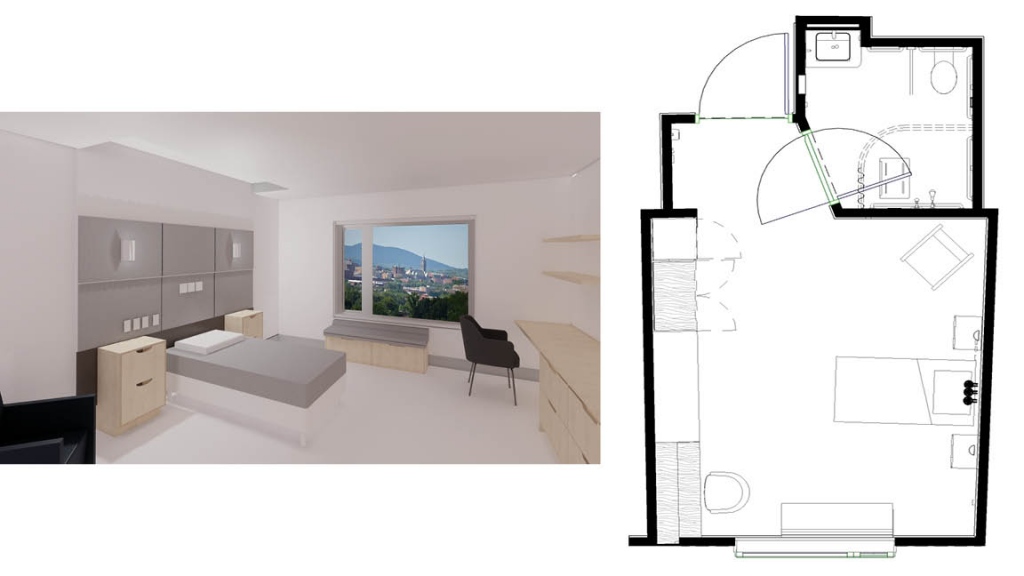
PAYETTE’s in house fabrication team recently completed a resident room mockup for the Soldiers’ Home in Holyoke, Massachusetts. The Soldiers’ Home is a new, long term care assisted living facility for Massachusetts veterans. The project includes 221 single rooms and 13 shared rooms. This facility is more than a healthcare building, it is the home for veterans in this community, which makes the residents’ bedrooms an integral part of the design. The mock-up provides an opportunity for residents, and their caregivers and families to experience their future home, and helps our team cater the design to meet their needs.
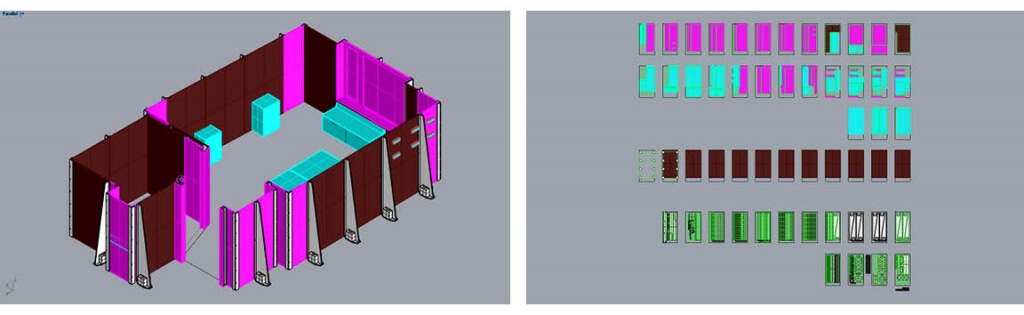
The fabrication team’s goal was to complete this endeavor entirely in house; and by doing so create a more efficient workflow with the design team and a more efficient mockup building process from conception to completion. We began with the design team working through iterations of a typical resident’s bedroom and providing the 3D model of the room to the fabrication team. The fabrication team was then able to develop and prepare a cut file of the mockup.
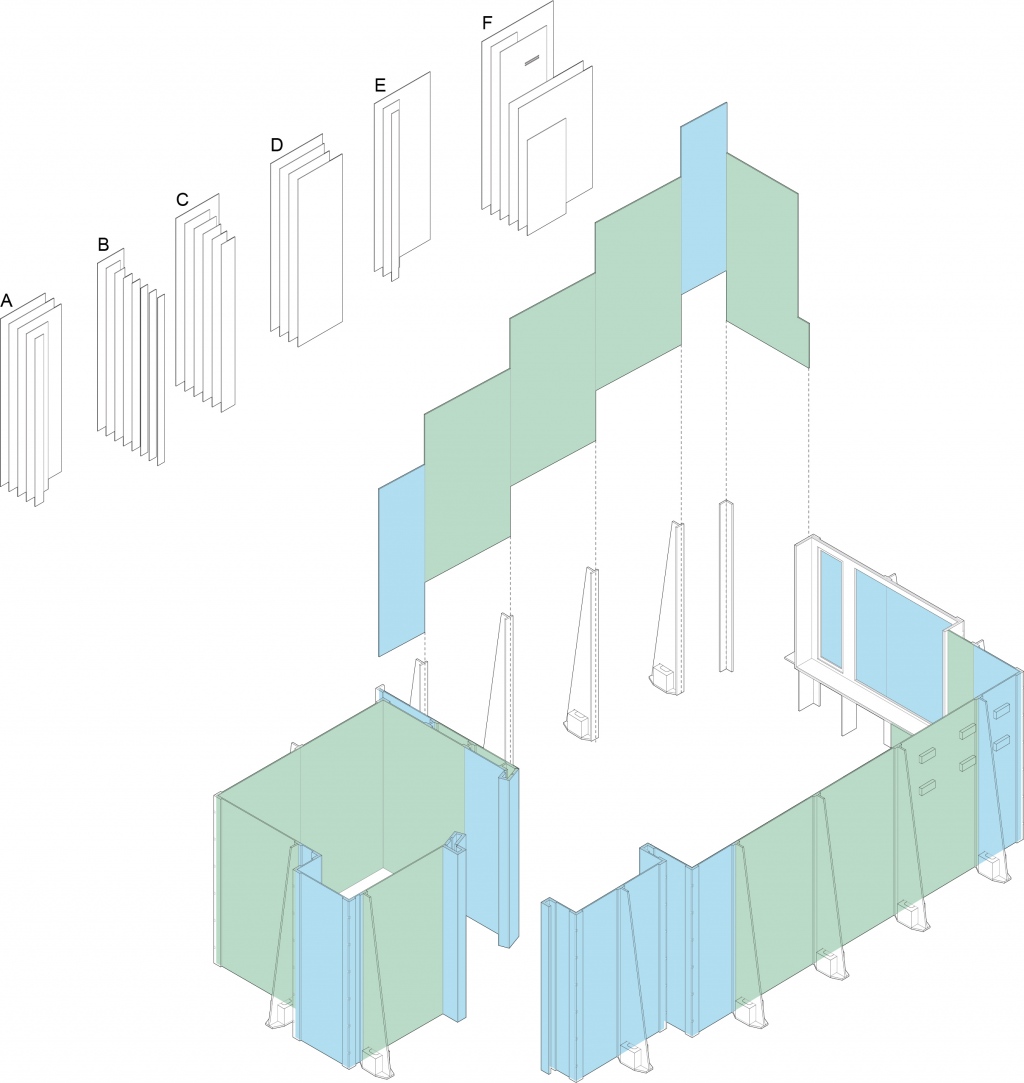
An elegant and efficient solution the fabrication team developed was a simple support system for the walls using typical pieces that could be CNC routed from plywood and easily assembled. This system included “spine” supports that would act as the connection for the Falconboard wall panels, as well as corner pieces that would help shape the room’s perimeter. These pieces were all pre-built in our in-house fabrication lab. The Falconboard wall panels were also CNC routed to size; there were two types of panels – the standard size and the varied size. A labeling system was implemented to ensure the boards were properly assembled. This process was very straightforward and made it easy to execute the construction.
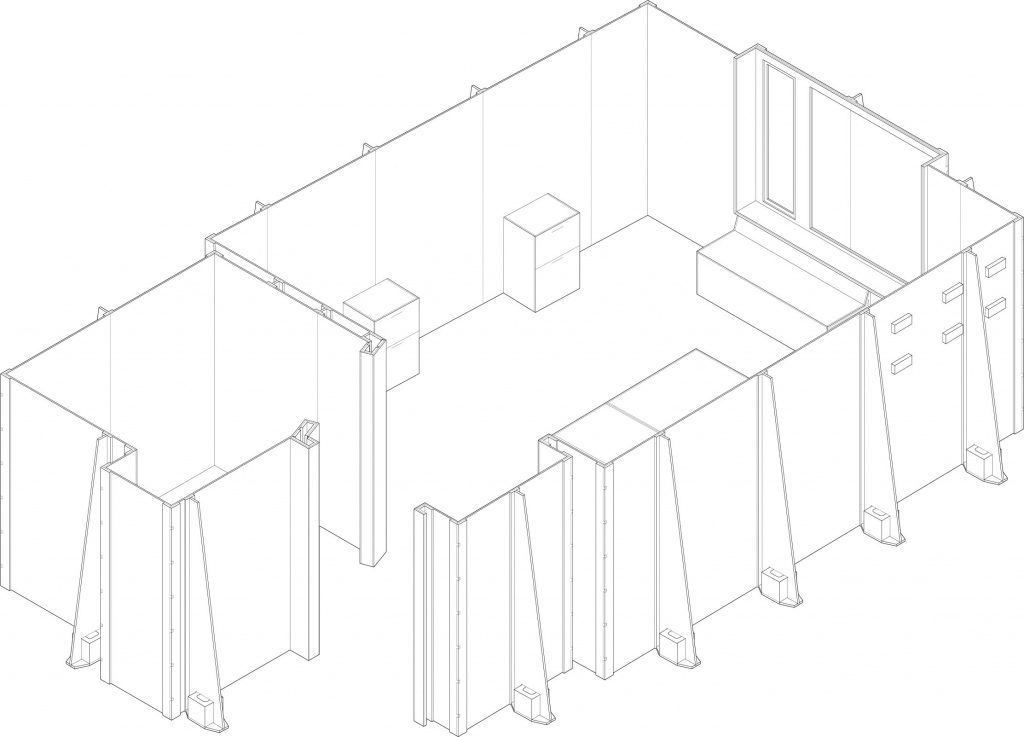
The millwork for the room was also pre-built in the Fabrication Lab using a combination of plywood and Falconboard cladding. The only element not pre-built was the window due to the size constraints for transporting the pieces to the site for final construction.
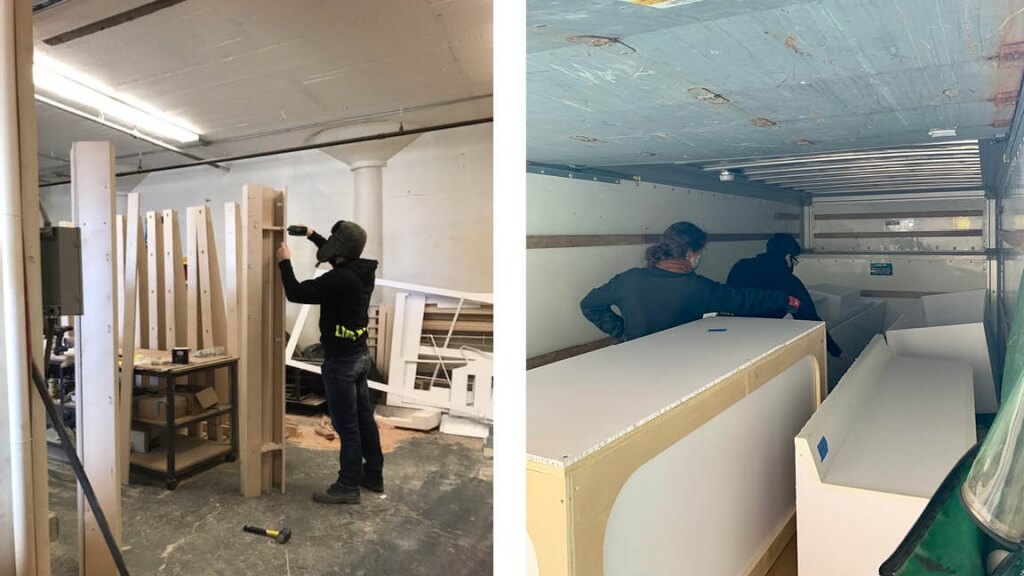
The on-site installation of the resident bedroom and bathroom was streamlined due to the preparation and system developed by the fabrication team. It was important to ensure the proper pieces were used in the correct spots, as well as making sure that the proper panels were flush with corners. The rest was simply holding panels in place and screwing them into the support. With three people working together, the room was assembled in one day on site.
The mock-up will be open for several weeks to obtain feedback on the design from the users. It has already started a dialogue between the design team and the clinical staff on workflow and opportunities to improve the design and develop creative solutions to meet their specific needs. The strength of our designs is enhanced when project teams can encourage user engagement, and room mockups do that.