The final installment in a 3 part series looking at the Penn State Health Milton S. Hershey Medical Center, Children’s Hospital Vertical Expansion project. You can read the first post, Delivering a Hospital During COVID Times, here and the second post, The New Women and Babies Center: an Integrated Care Model here.
Building on top of an existing building is a complex – and costly – endeavor. When the existing building is a hospital facility, the challenge becomes more formidable. So why did Penn State Hershey decide to add a 140,000 square foot inpatient facility on top of the existing Children’s Hospital? The answer is schedule.
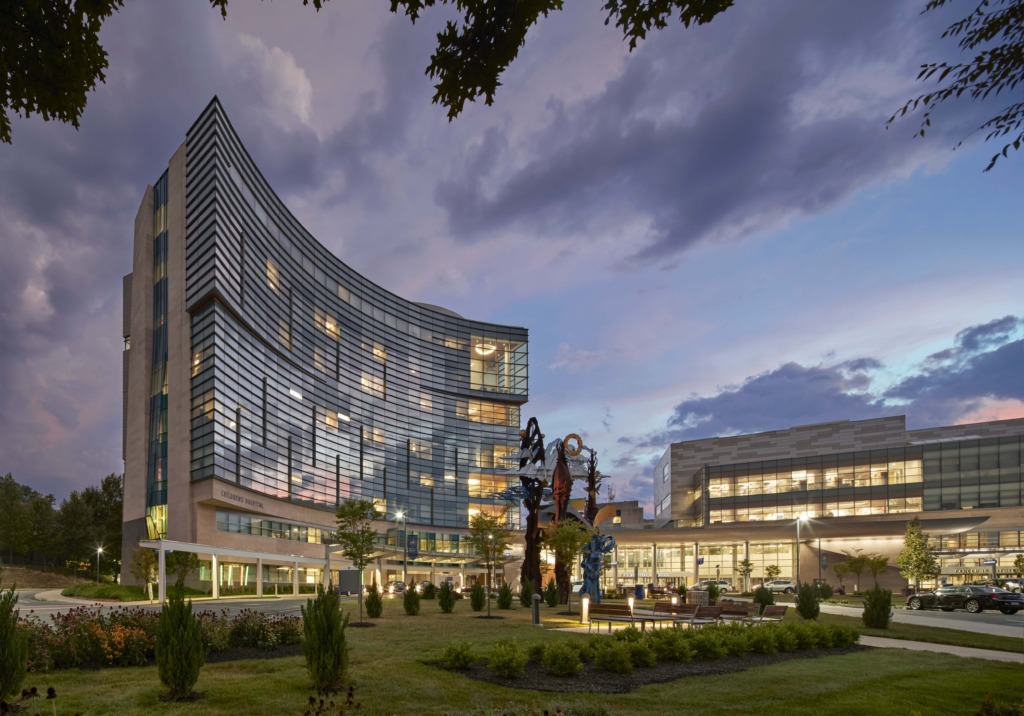
Photo Credit Robert Benson Photography
The 2002 Facility Master Plan identified the need for inpatient beds as the highest priority to address capacity issues and “right sizing” of patient rooms. It was determined that time was of the essence. It was paramount to Penn State Health that additional patient rooms in the Women and Babies Center be brought online as quickly as possible. At the time, facility capacity exceeded 95% on a continuous prolonged basis. Hershey Medical Center was routinely in “divert status” and not able to accept patient transfers. Bringing additional beds online was not only imperative to meeting the needs of the community but would be essential to generate additional revenue, which was projected to be $5M+ monthly, helping to cover the cost of the construction.

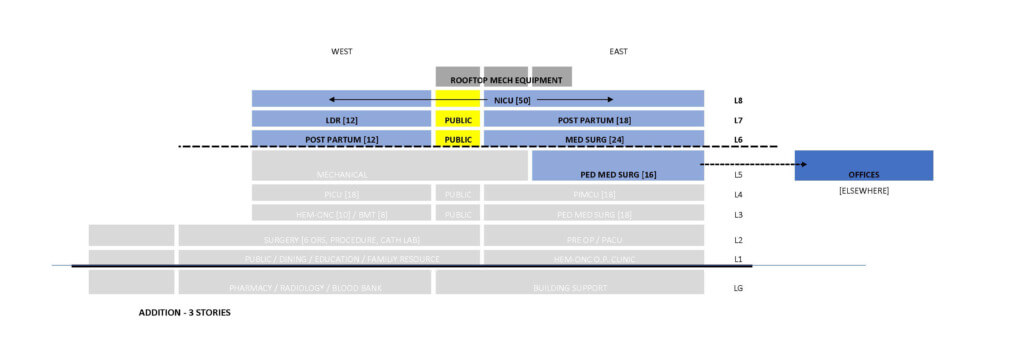
Program Stacking
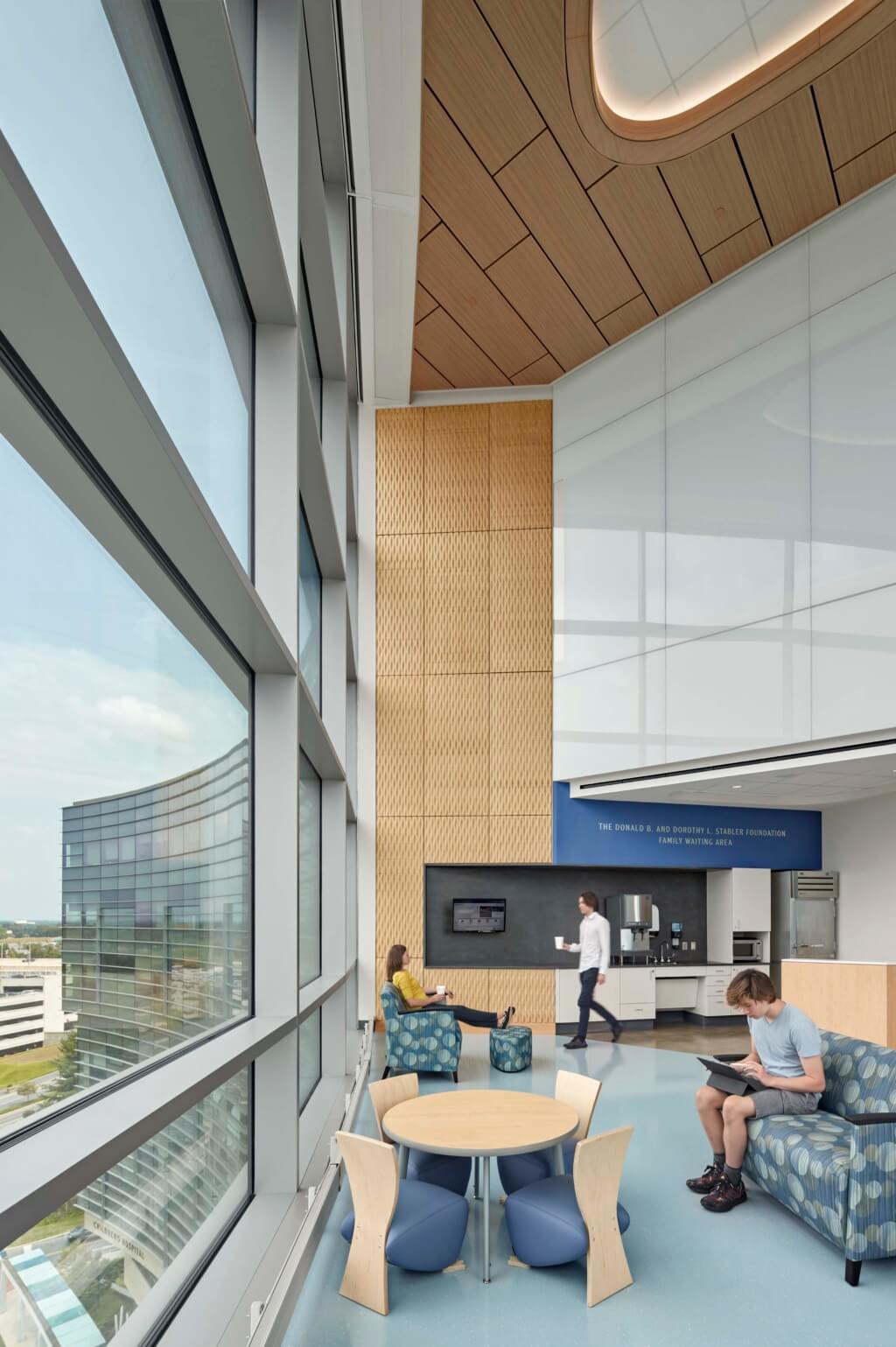
Photo Credit Robert Benson Photography
In 2017, barely five years after the completion of the Children’s Hospital building, Penn State Health leadership decided to proceed with a Vertical Expansion of the Children’s Hospital. The project team established an aggressive 36-month schedule for design and construction, which was endorsed by the entire team. The vertical expansion on top of an existing footprint reduced the typical Land Development municipal regulatory process by approximately a year. Additionally, this strategy eliminated the need for the conventional site preparation, site utility/infrastructure work and foundation construction, starting the construction sequence with structural steel erection. Therefore, a vertical expansion solution was chosen as the most expedient means to bring additional patient rooms on-line.
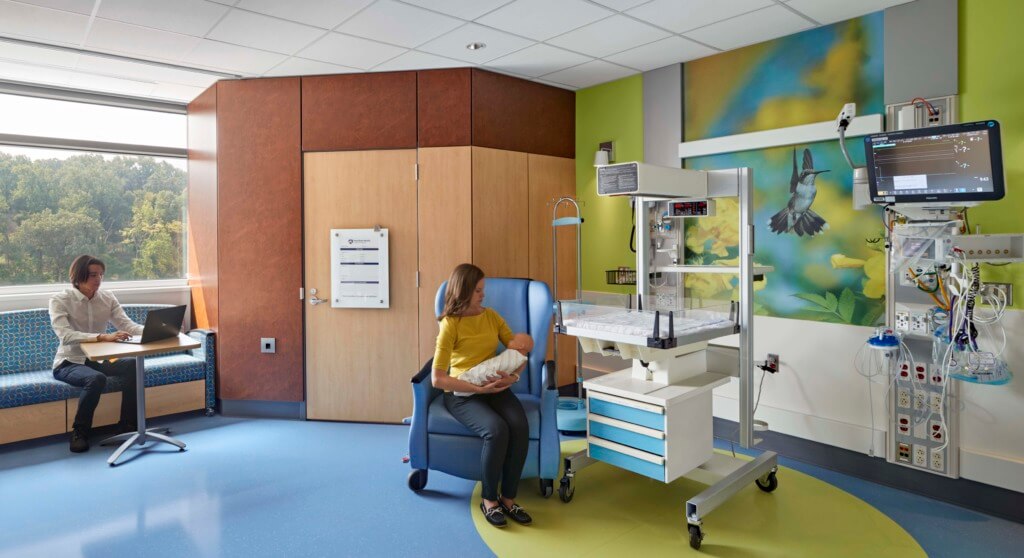
Photo Credit Robert Benson Photography
Preparing for a Vertical Expansion
As early as the 2002 Master Plan, Penn State Health knew they wanted to bring together women’s services and the Neonatal ICU. This would provide peace of mind for new parents worried about their infants in the NICU. Strengthening those bonds and easing those stressors go a long way in the healing process for both mother and baby. As the Children’s Hospital was planned, however, this was not able to fit the budget. Instead, it was decided that a future expansion to the Children’s Hospital would realize a robust, comprehensive, and state-of-the-art Women and Babies Center. This project brought that plan to life.
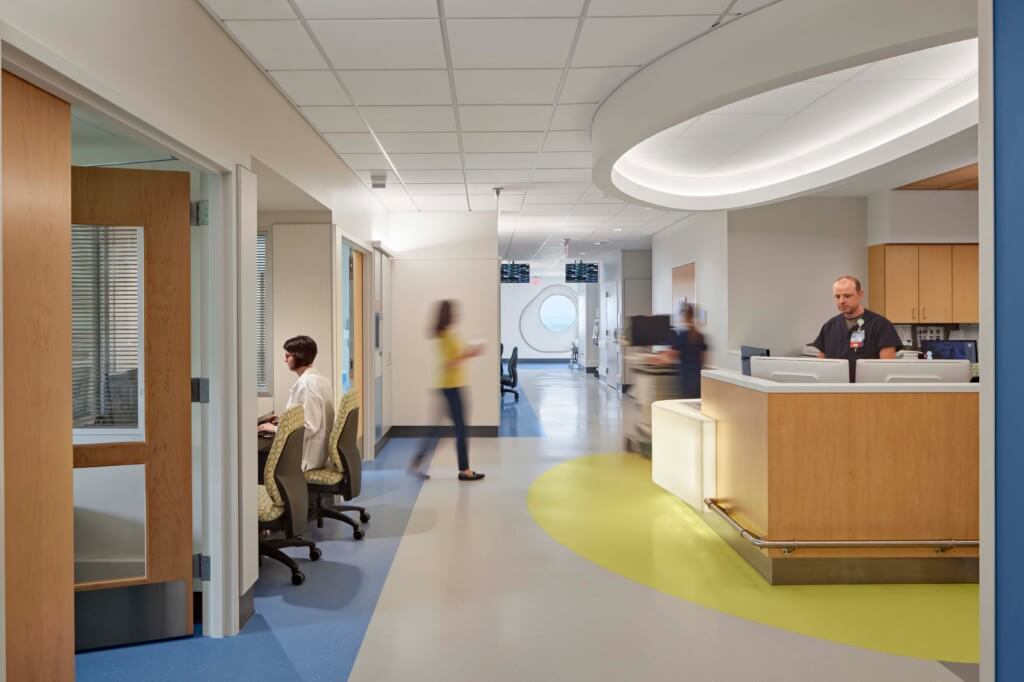
Photo Credit Robert Benson Photography
Thus in 2008, the Children’s Hospital was designed with a vertical expansion in mind. The planning of a future vertical expansion was carefully mapped out to minimize the interruption of the hospital operation and to satisfy safety and comfort during the construction. A set of technical provisions during the design of the 5-story base building included life safety features for a high-rise facility, logistics and materials handling services, enhanced structural design and extra elevator shafts.
The program stacking in the Children’s Hospital anticipated a vertical addition. A mechanical penthouse and an office/administration suite were located on the top level 5, serving as a buffer during the vertical expansion. The construction activities over the existing roof would not be directly above patient care spaces, minimizing noise and vibration during construction.
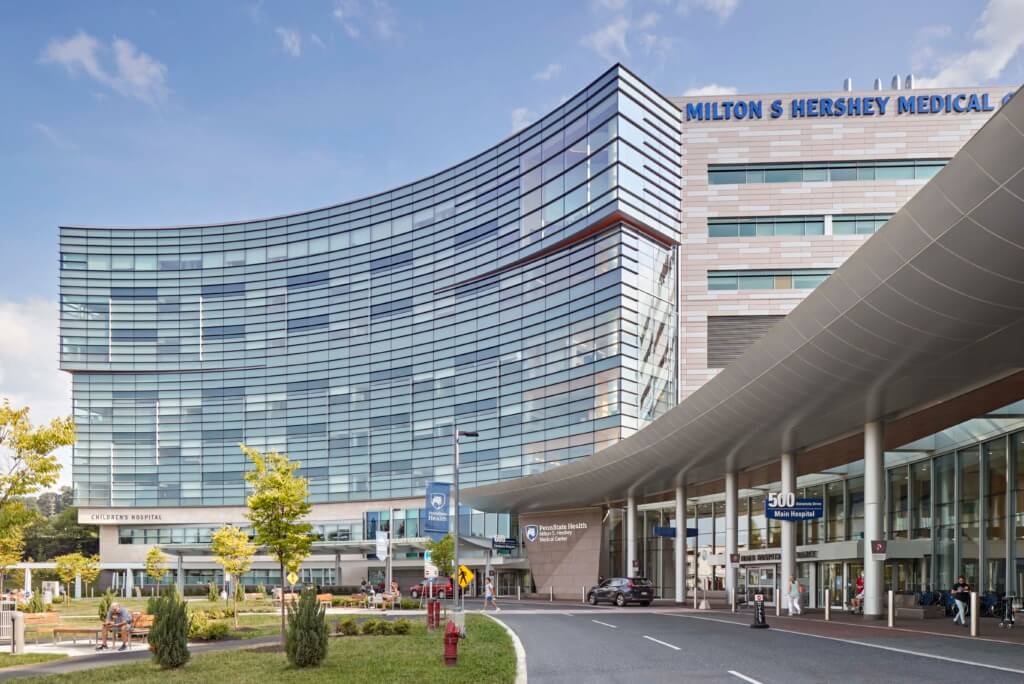
Photo Credit Robert Benson Photography
Delivery Method
From the beginning, the theme of the project was “speed to market.” The process started with the creation of a Team Collaboration Charter to ensure expectations were clear to all from the outset. To further expedite delivery, the project was divided in two phases: Core and Shell, and Fit-out. Documents were first issued for Shell and Core, so that construction could begin on the steel frame and building envelope while interior fit-out design for clinical programs was completed. Whiting-Turner, the construction manager, orchestrated the release of multiple construction packages to onboard design/assist partners for structural steel, mechanical, plumbing and electrical work. Working closely with the A/E team, these trade partners were able to aid in the completion of the Contract Documents, while beginning procurement of long lead items and critical materials to allow the project to progress in the field.
This article was developed jointly with Gino Ciotola, Senior Project Manager, The Whiting-Turner Contracting Company, and Carolyn J Stoner, Project Director, Penn State Health