Part three of a series highlighting recent fume hood research by Andrea Love, Ron Blanchard, Michael Mandeville and Luke Laverty exploring the potential for energy savings through a better understanding of minimum fume hood flow rates and diversity factors for high-intensity labs.
As discussed in part two, lower fume hood face velocities can have a significant impact on the exhaust air used by a fume hood. During our research, we contacted a number of fume hood manufacturers typically specified on PAYETTE projects and compiled pertinent information on their High Performance Fume Hoods. A portion of the data subsets queried included the exhaust volume in cubic feet per minute (CFM) required to meet ASHRAE 110 containment testing for hood widths of 4’, 5’, 6’ and 8’ with vertical sashes fully open and 18” open (typical operating height) at face velocities of 100, 80, 60, 50, and even 40 feet per minute (FPM).
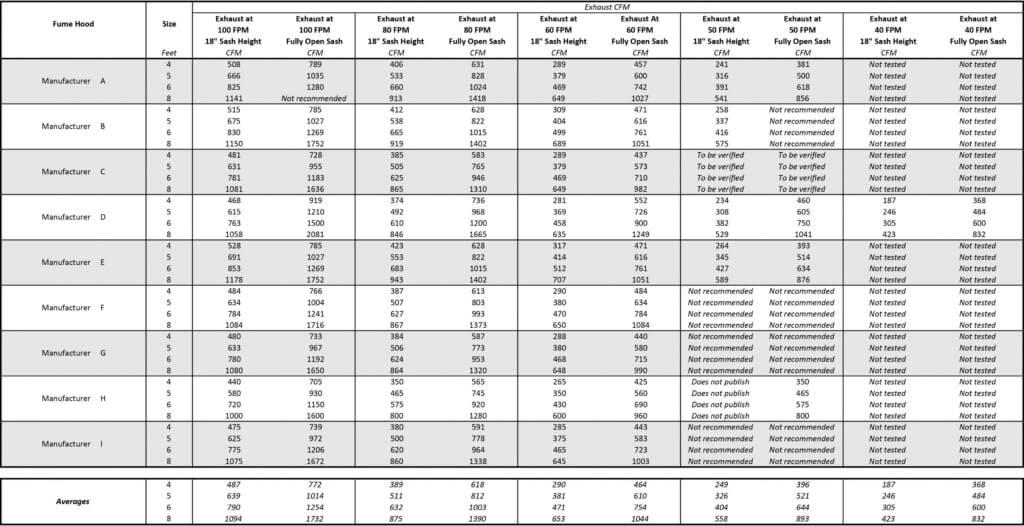
Manufacturers’ High Performance Fume Hood exhaust volume requirements (PAYETTE)
As expected, exhaust volume is substantially reduced when face velocity drops from the more traditional 100 FPM to the new recommended low of 60 FPM; however, we discovered that not all manufacturers are equal in terms of how much exhaust air they require to provide adequate containment. For example, a 6’ fume hood operating at 60 FPM with an 18” open sash yields an exhaust range from as low as 430 CFM for Manufacturer H up to 512 CFM for Manufacturer E, a nearly 20% difference in exhaust volume. Additionally, not all manufacturers offer the same potential for exhaust reduction; three manufacturers test and publish results down to 50 FPM face velocities while Manufacturer D even publishes the ability to achieve containment at 40 FPM. As discussed in the previous post, these sub-60 FPM face velocities require additional scrutiny to confirm they meet the ASHRAE 110 “As Used” containment test. Although these high-efficiency fume hoods may come with a higher price tag (one manufacturer noted a premium of 20% compared to their standard hood), the long term savings should far outweigh the initial cost impact. Reducing face velocity from 100 FPM to 60 FPM could save as much as $1,217 in operating costs per year for each fume hood, which is a worthy investment considering the life span of the hood, especially when multiplied by the substantial fume hood counts typically found in our science and research centers. [1]
While designers can impact energy savings through informed fume hood selection and exhaust volume calculations, there is an additional reduction attainable by closing the fume hood sash when not in use. Institutions across the country have spearheaded a “Shut the Sash” campaign to educate users on the energy savings and benefits to general lab safety by closing the sash when done working. A seminal white paper by Harvard University aimed to quantify this impact on a number of existing laboratories on campus. The study determined that when a fume hood’s sash is closed while not in use, whether through an automatic sash closer or a targeted campaign imploring users to shut the sash manually, there is substantial energy savings from an average of 409 CFM (when the sash is left open) to 250 CFM (with manual sash closing) and 231 CFM (with automatic closers). Totaled across all fume hoods and buildings in the study, the university is saving more than $200,000 per year in energy costs with a greenhouse emission reduction of over 300 Metric Tons Carbon Dioxide Equivalent, equal to the carbon sequestered by 353 acres of U.S. forests in one year. [2,3]
Energy savings with a closed sash is enabled by the exhaust setbacks identified in section 3.3.2 of ANSI/AIHA Z9.5-2012 Laboratory Ventilation, which states a minimum fume hood flow rate in the range of 150 to 375 hood air changes per hour (ACH).[4] As seen in the table below, the same 6’ wide Manufacturer H hood highlighted earlier, which requires 430 CFM when operating at 60 FPM with an 18” open sash, can be set back to 117 CFM using the low end of the Z9.5 range, a significant 73% in energy savings.
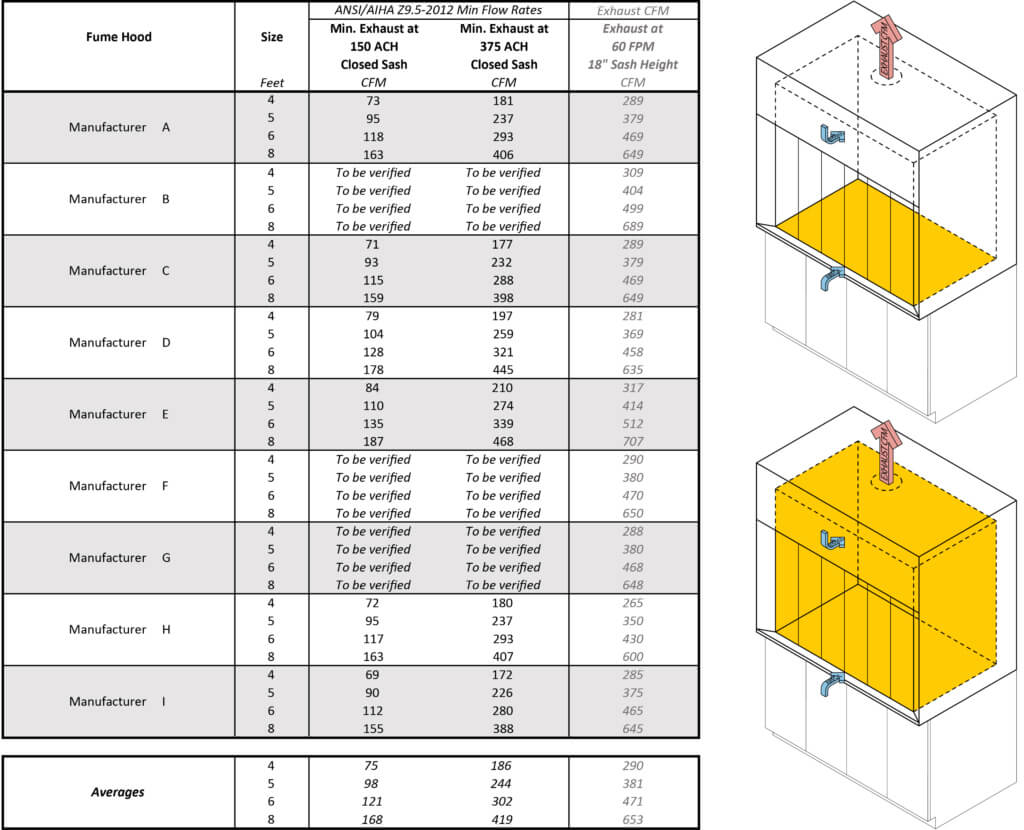
Manufacturers’ High Performance Hood minimum exhaust requirements and comparison diagram of the calculations based on the interior hood work surface for NFPA 45-2004 (top right) versus the interior hood volume for ANSI/AIHA Z9.5-2012 (bottom right)
We reached out to the Z9.5 subcommittee to better understand the rationale for listing a range as opposed to a single minimum exhaust requirement; however, they do not provide technical feedback or interpretation of their standards. To the best of our knowledge, the high-end of the range is a holdover from the previous fume hood exhaust standard listed in NFPA 45-2004 which required an exhaust rate of 25 CFM per square foot of interior hood work surface (section A.8.4.7). [5] The 25 CFM/SF exhaust, when converted to an interior volume to be consistent with Z9.5 calculations, is equal to the range’s high end of 375 ACH. It should be noted, however, that as of 2011, NFPA 45 no longer lists exhaust criteria and instead defers entirely to the requirements of Z9.5. As Z9.5 lists a lower limit than the old NFPA 45, and the revised NFPA 45 no longer defines a recommended exhaust, it is conceivable that the high end of the range may be removed in future versions. While the ambiguity of the range exists, engineers tend to default to exhaust volumes at the upper end. By educating ourselves on the requirements and background of Z9.5, we should push our engineers to review their calculations and work with EH&S groups to reduce exhaust volumes toward the lower 150 ACH number to achieve maximum energy savings.
Part four will follow further highlighting the importance of closing the sash and the impact it can have on the building’s overall air system through fume hood diversity factors.
[1] Fume Hood Calculator
[2] Gilly, Quentin. “Validating Cost and Energy Savings from Harvard’s Shut the Sash Program.” Harvard University, Pg. 5.
[3] Green House Gas Equivalencies Calculator
[4] ANSI/AIHA Z9.5: Laboratory Ventilation, 2012 Edition
[5] NFPA 45: Standard on Fire Protection for Laboratories Using Chemicals, 2004 Edition
Related Links:
Low Flow is the New Norm: Part 1
How Low can You Go?: Part 2